Finished car photos; restoration details follow: Click any image to start slide show.
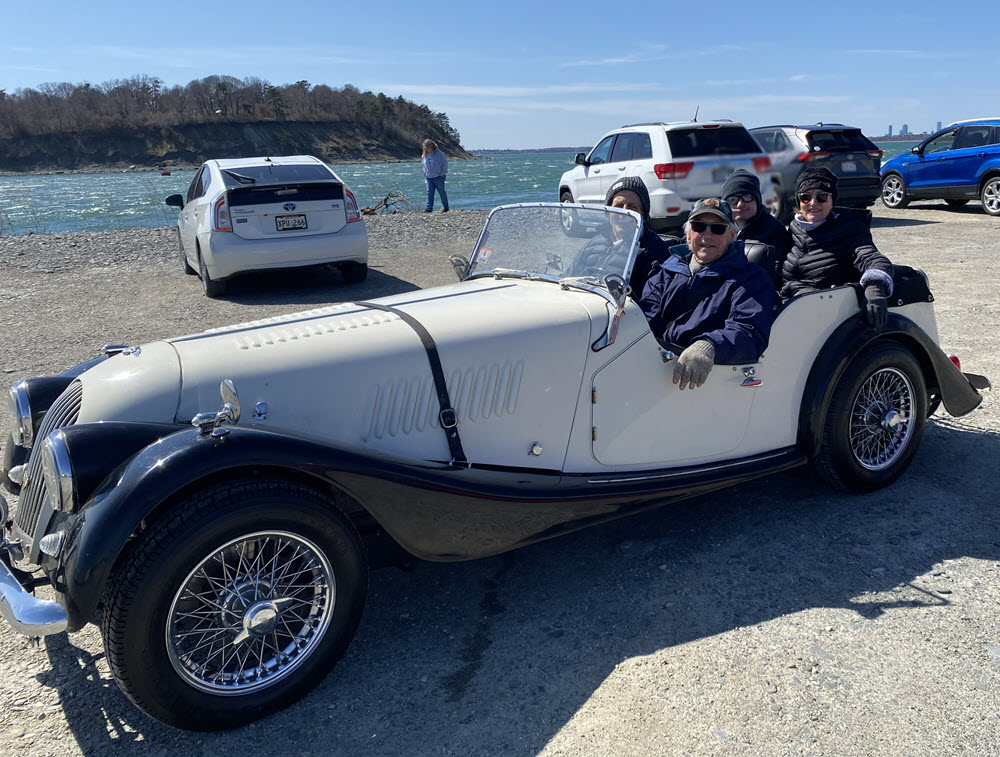
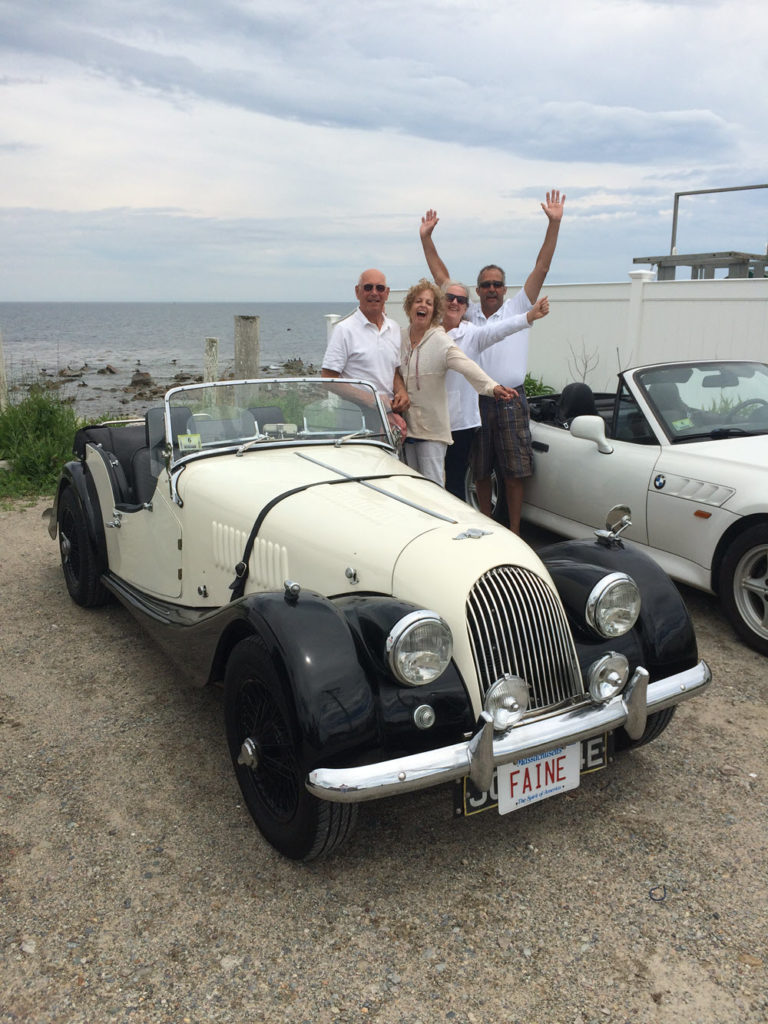
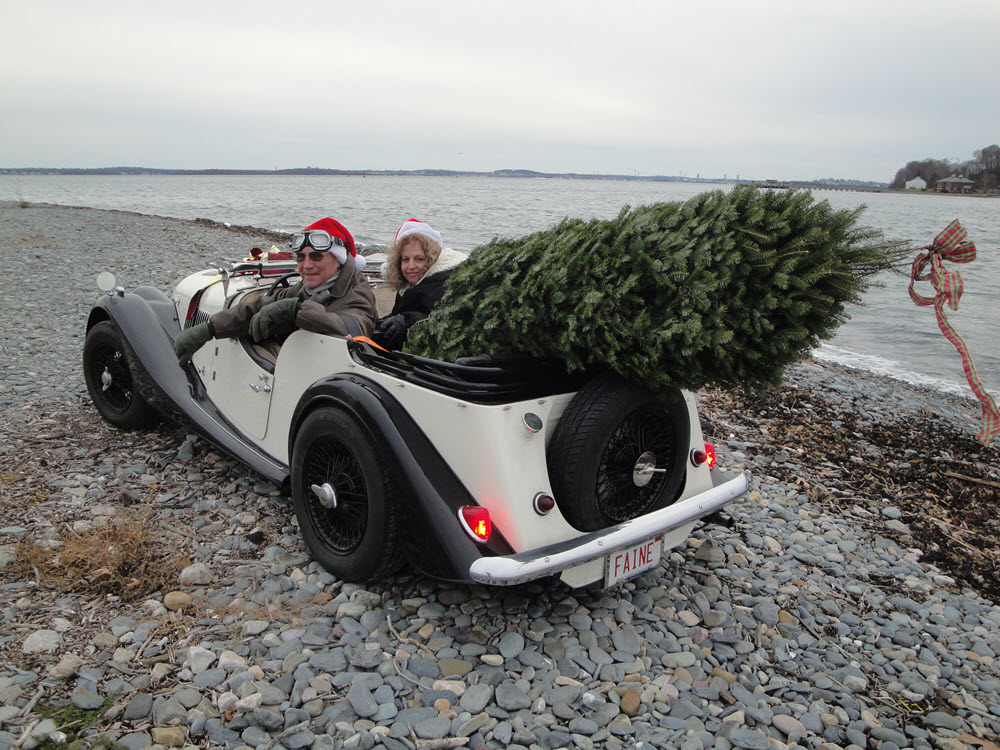
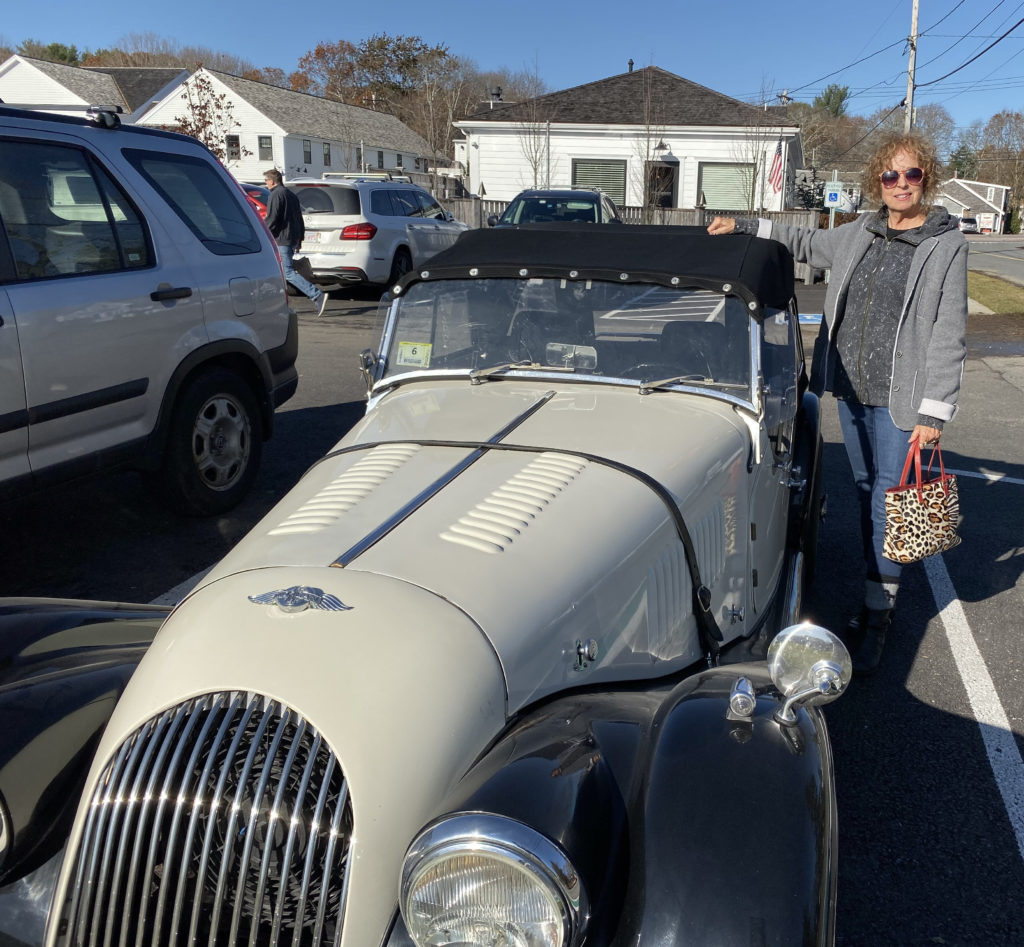
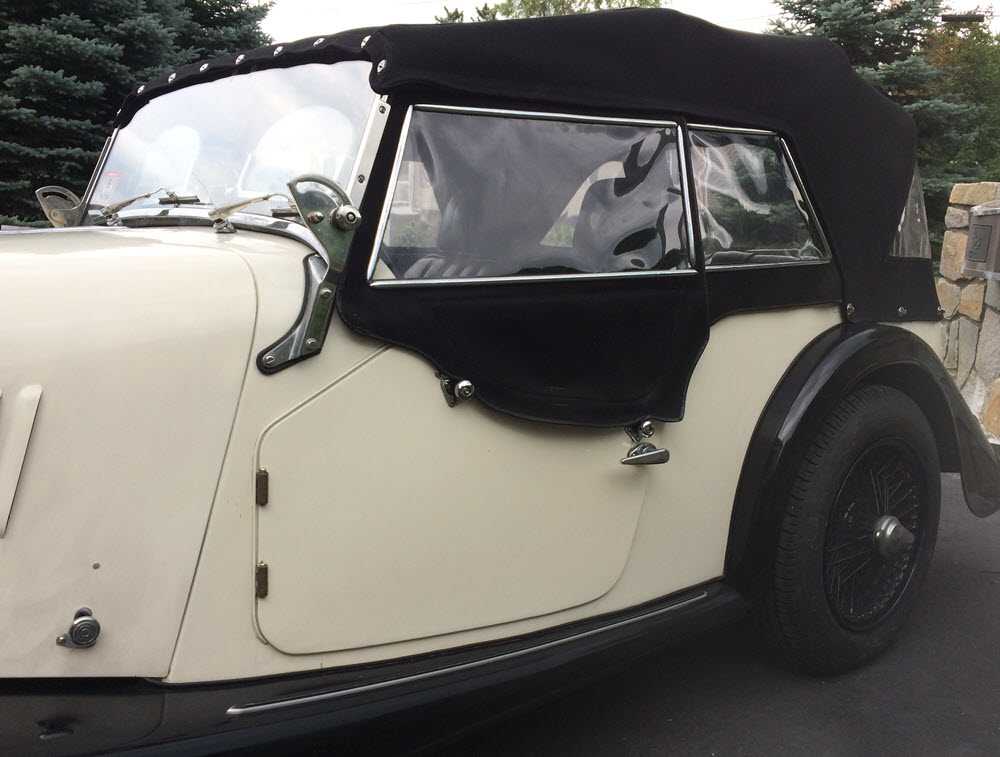
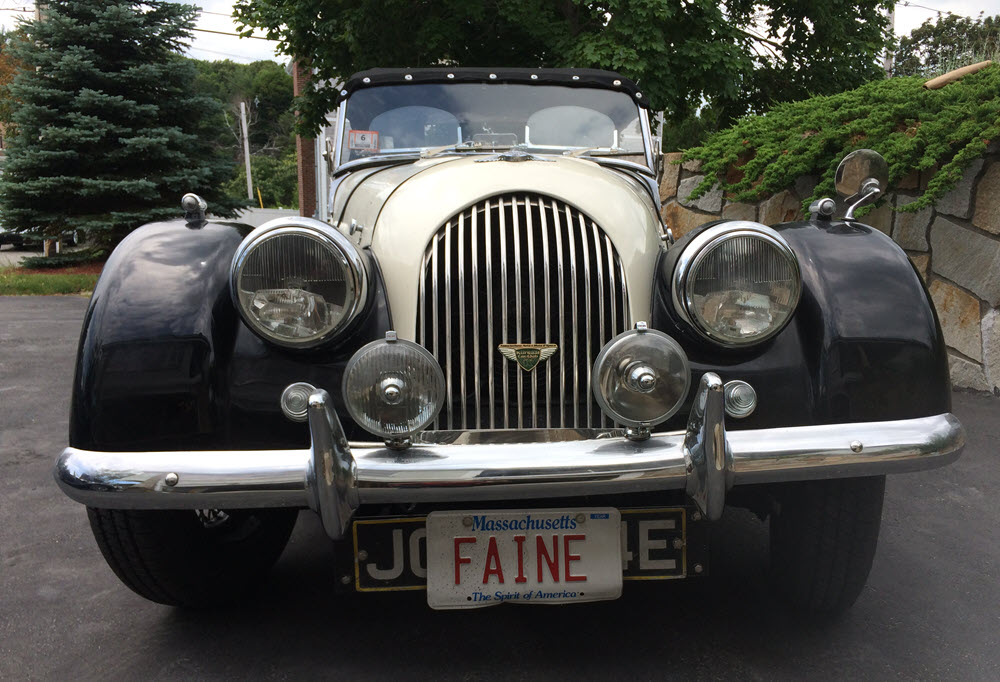
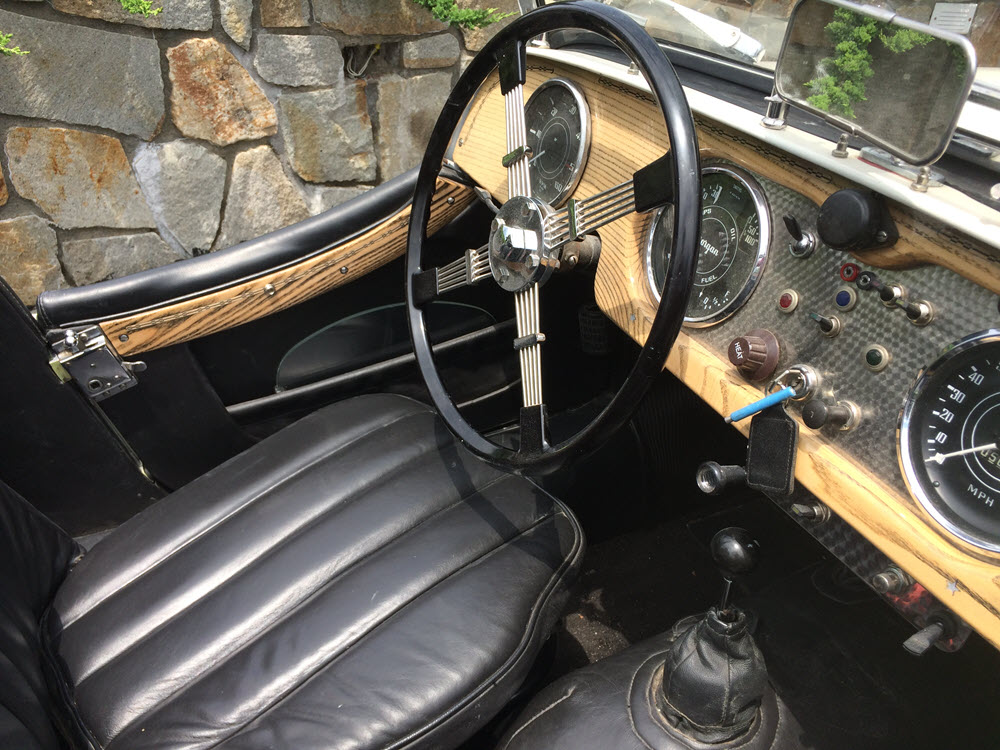
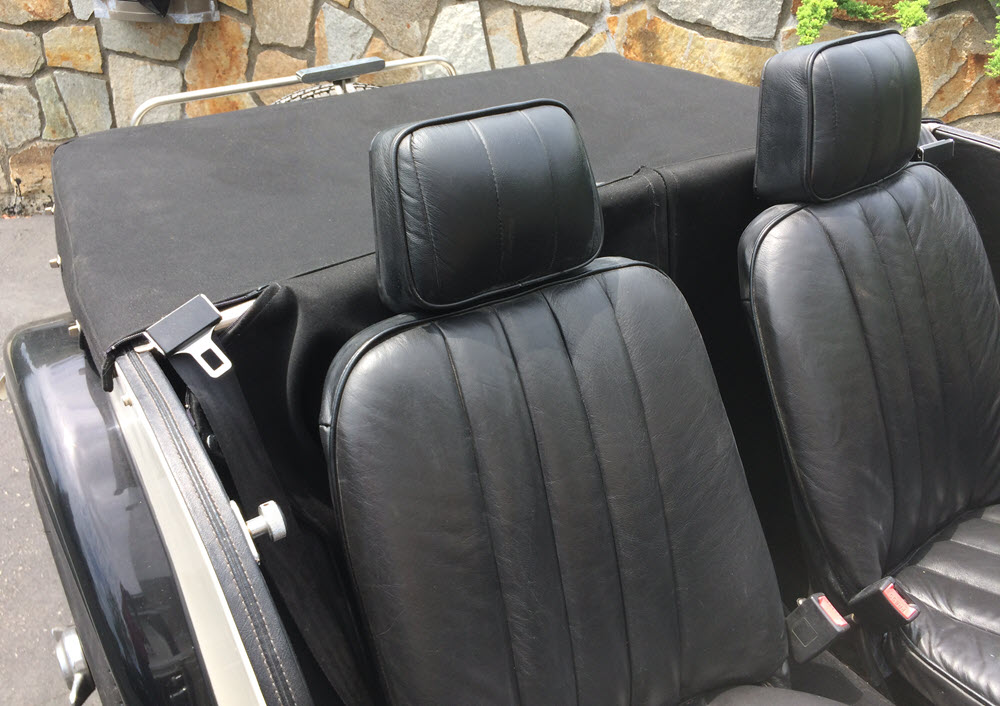
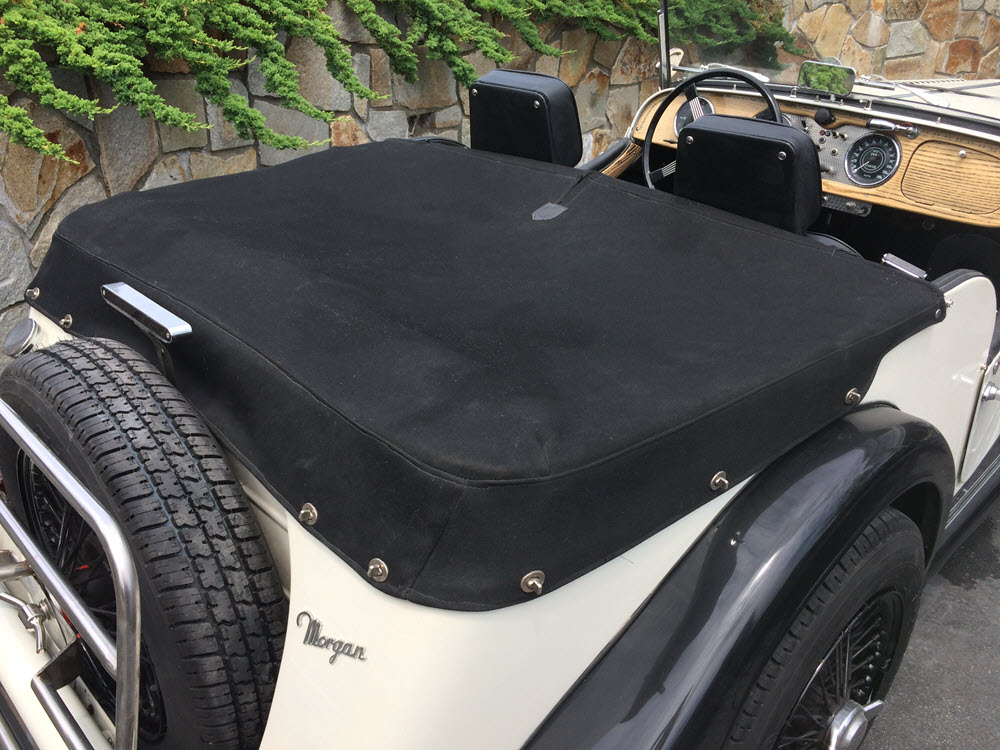

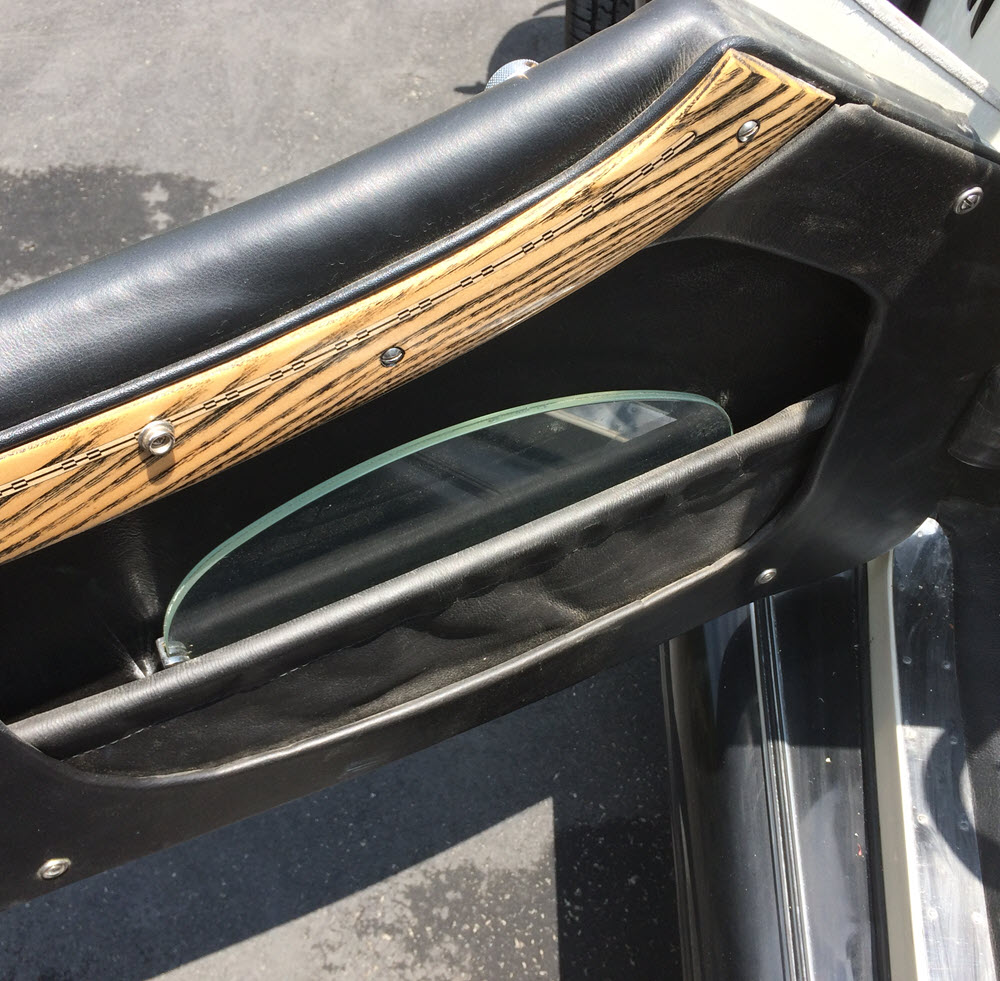
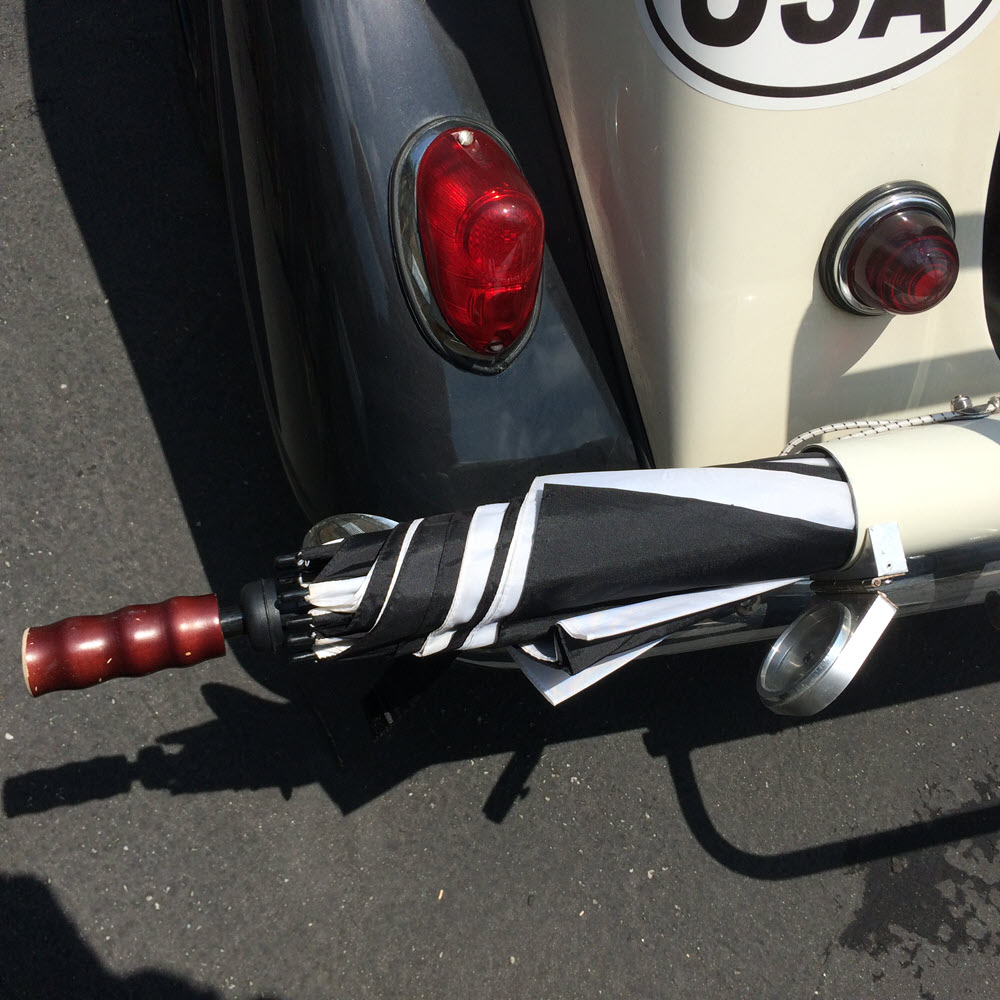
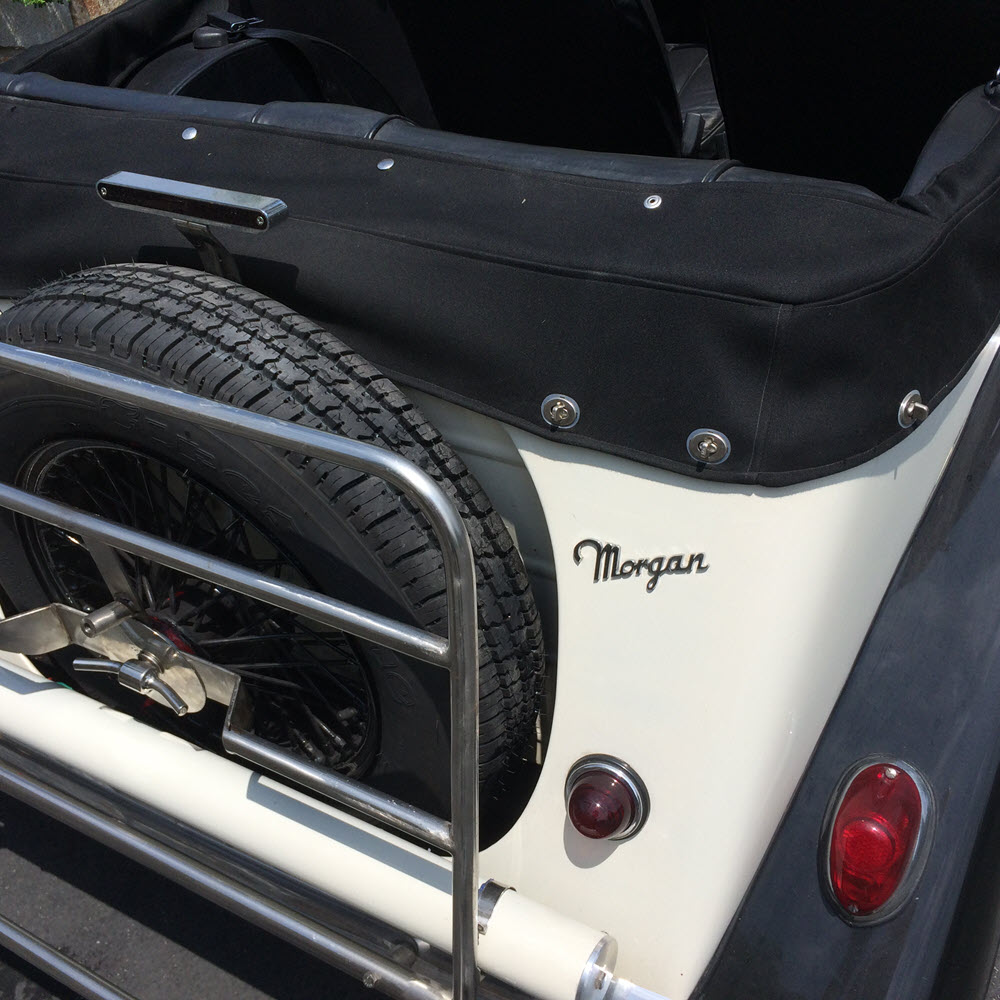
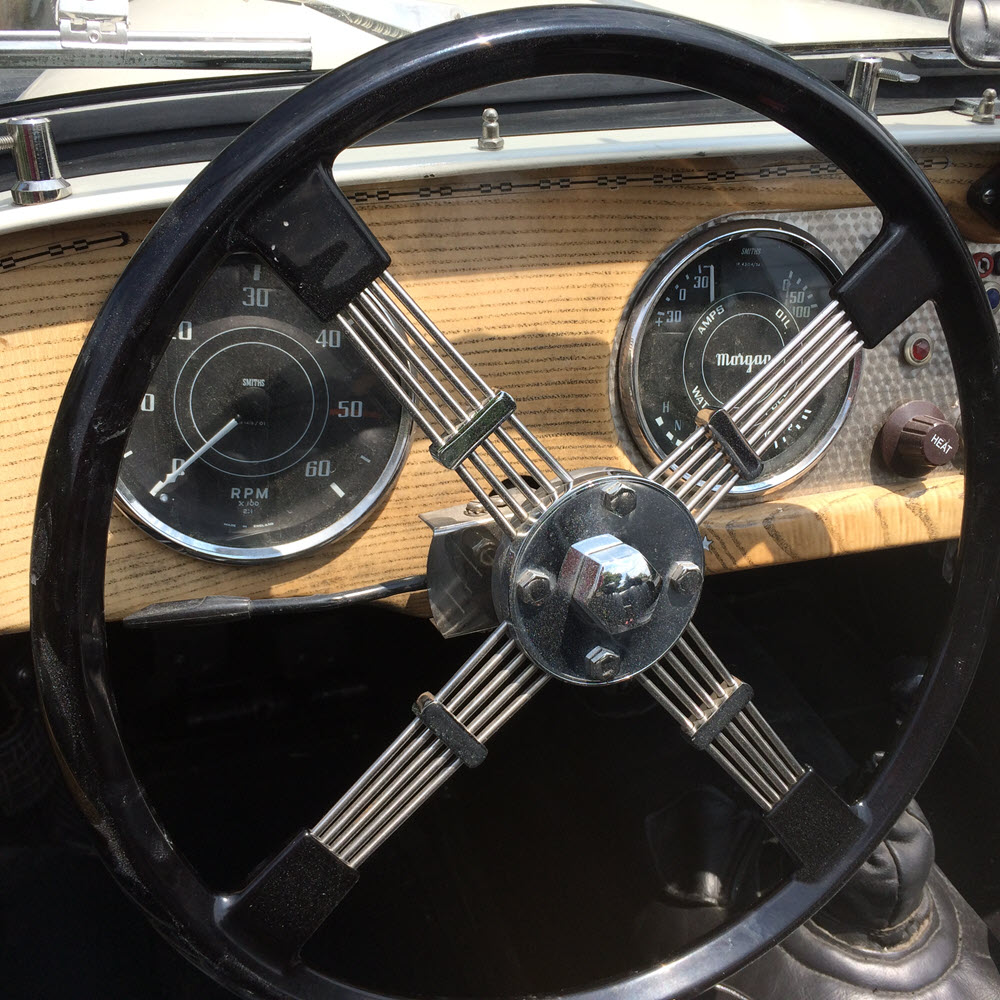
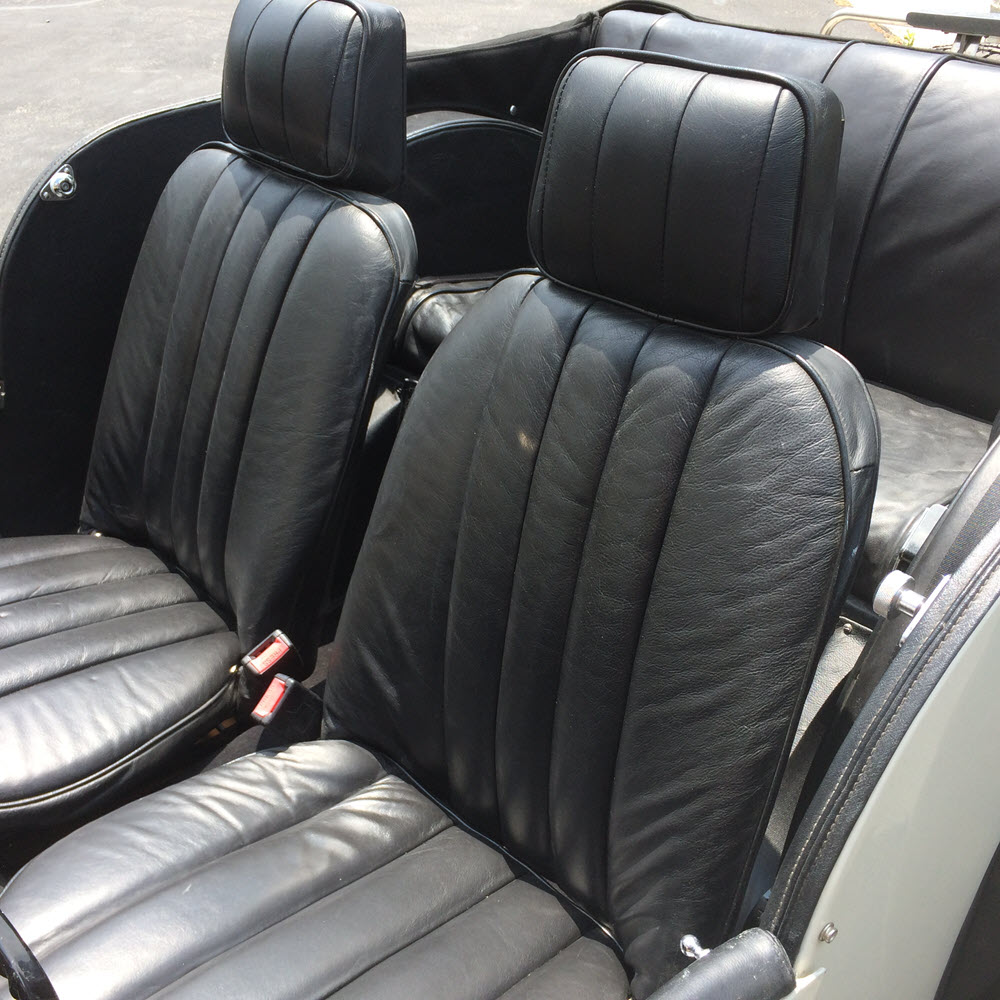
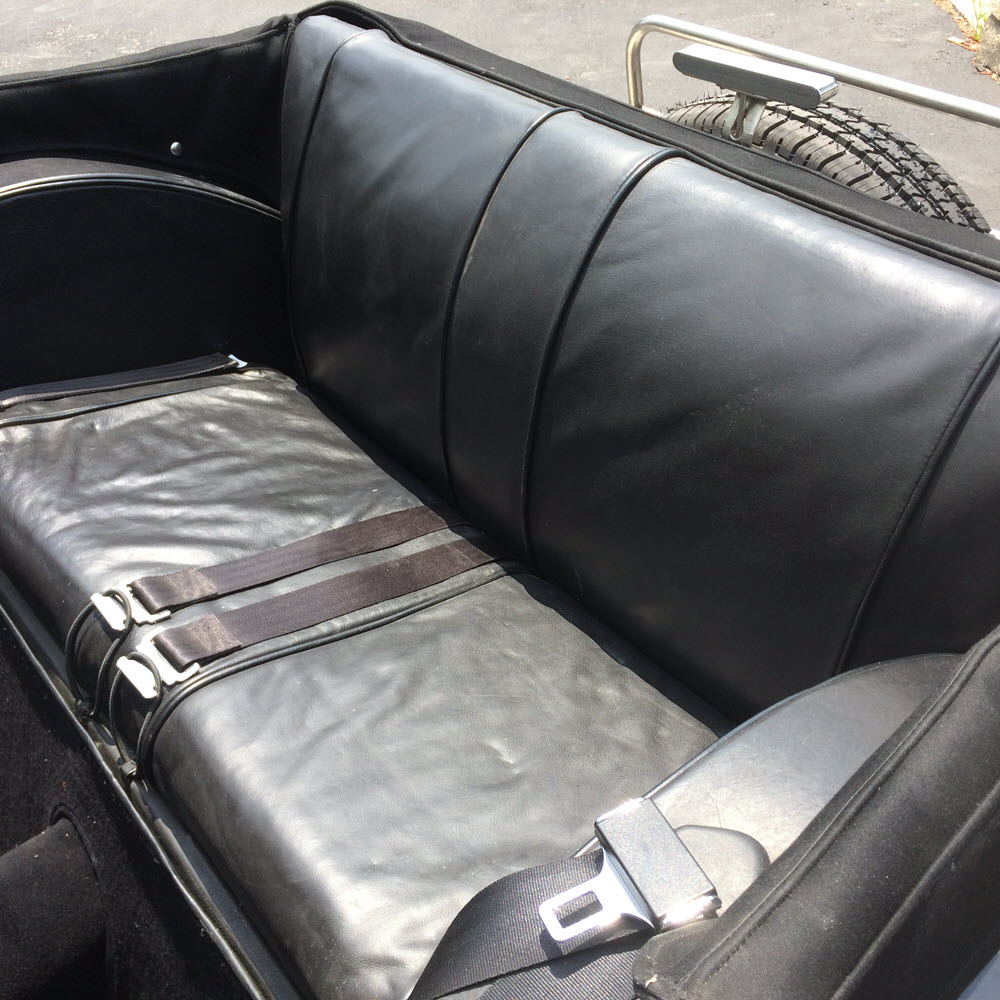
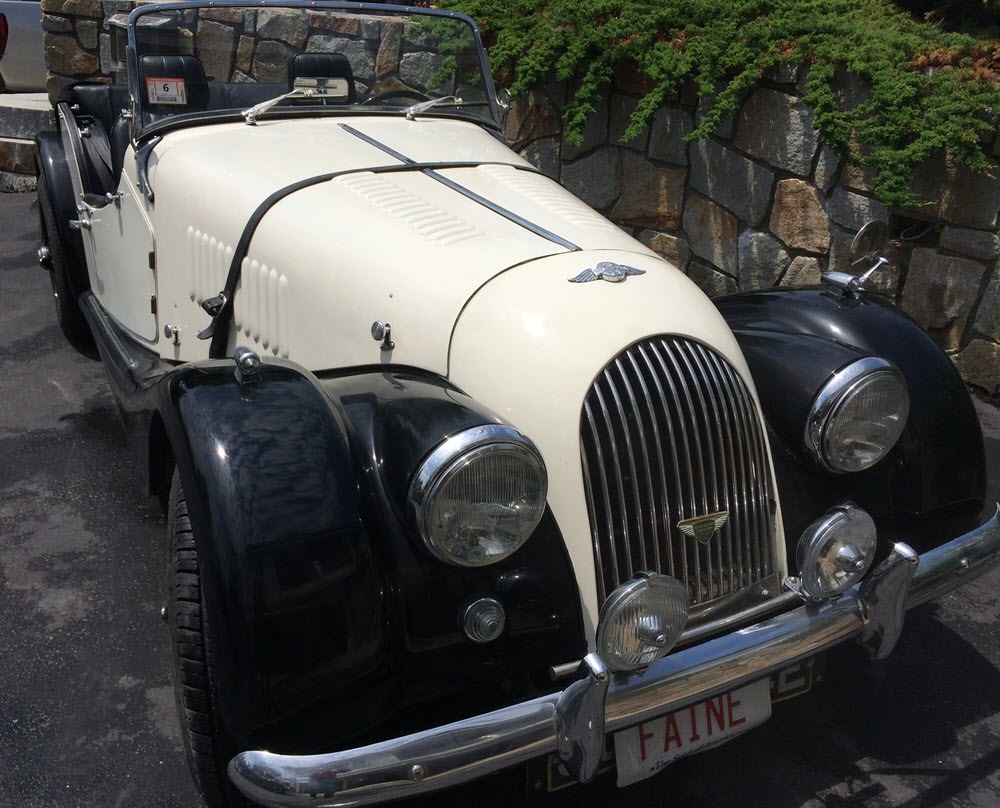

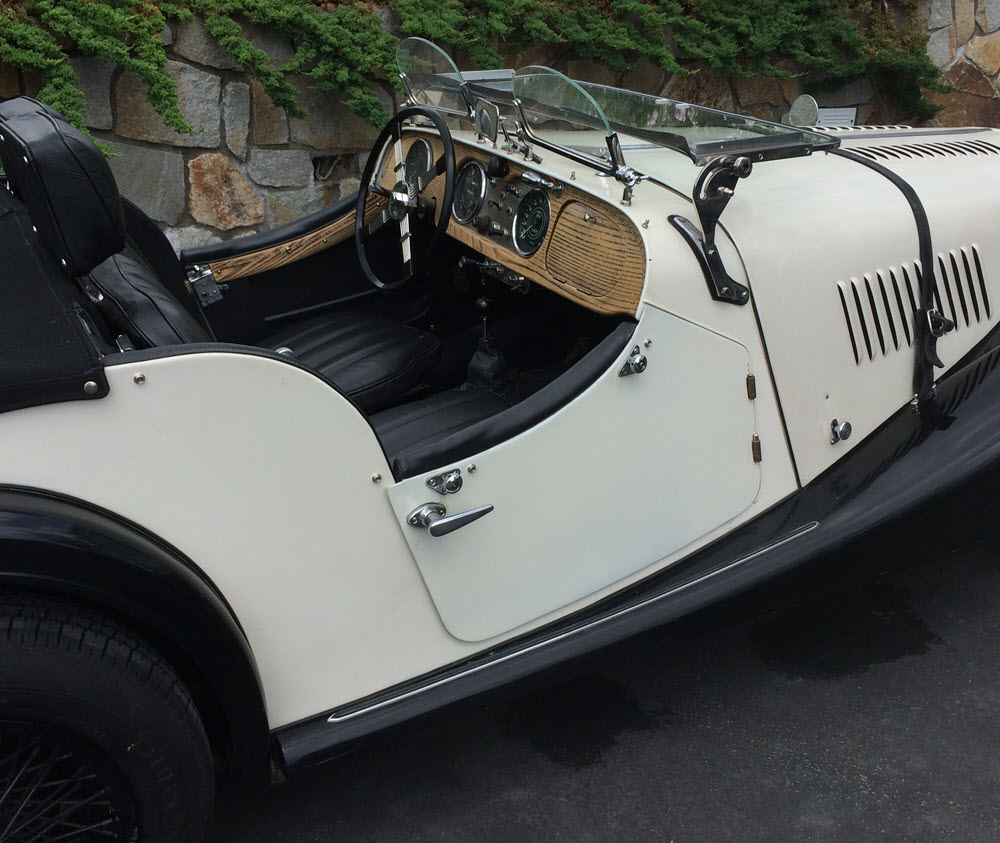
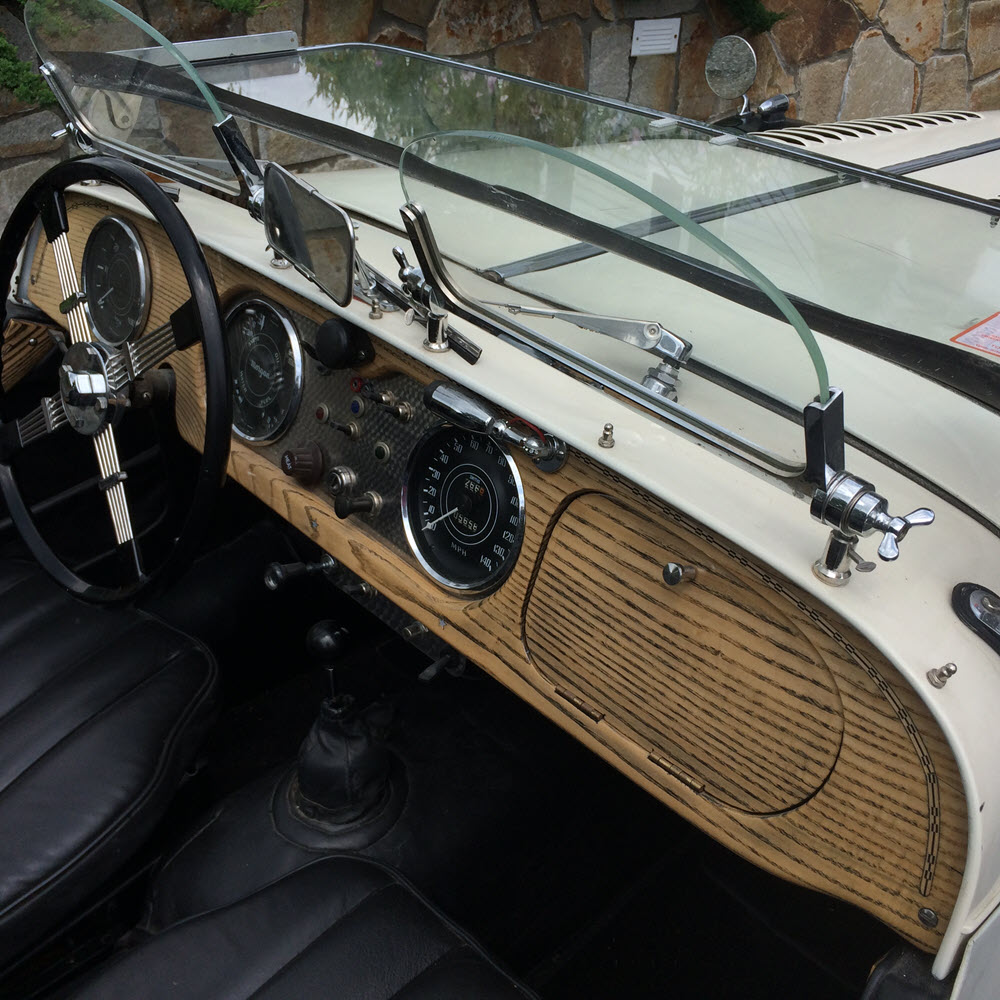
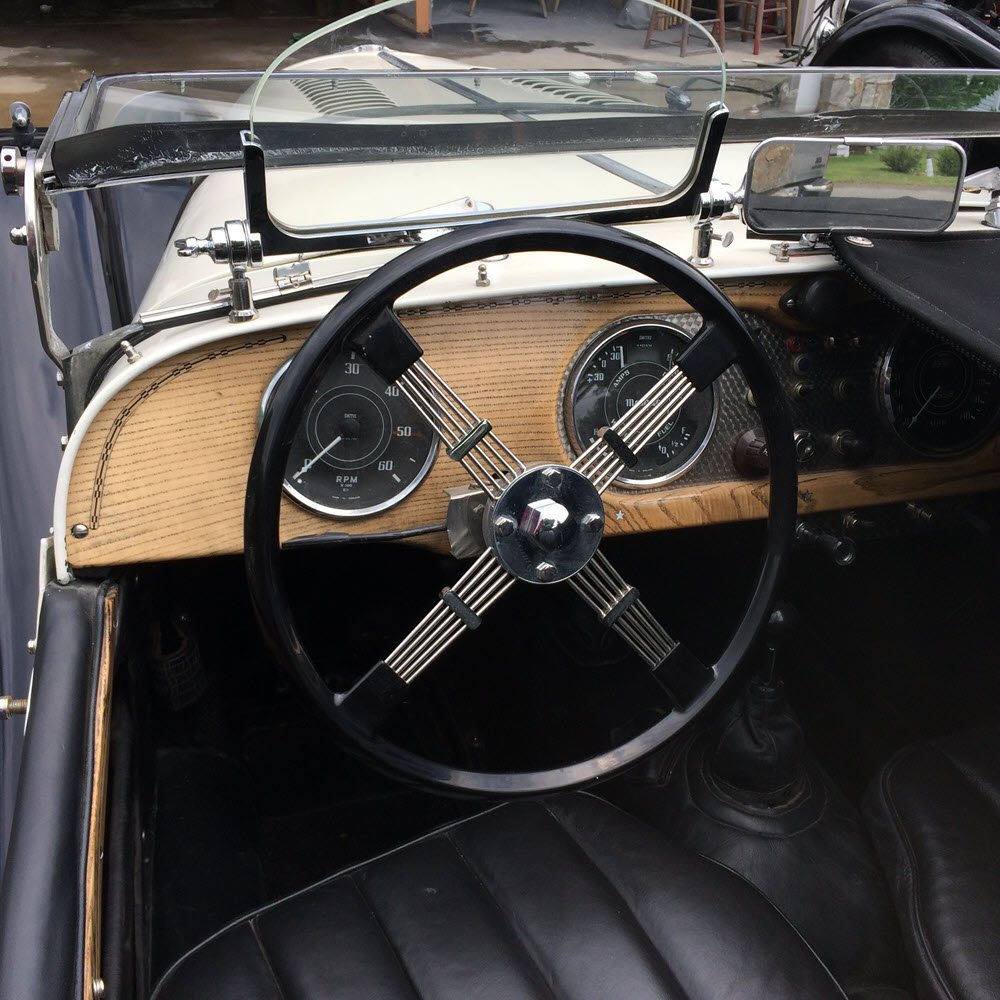
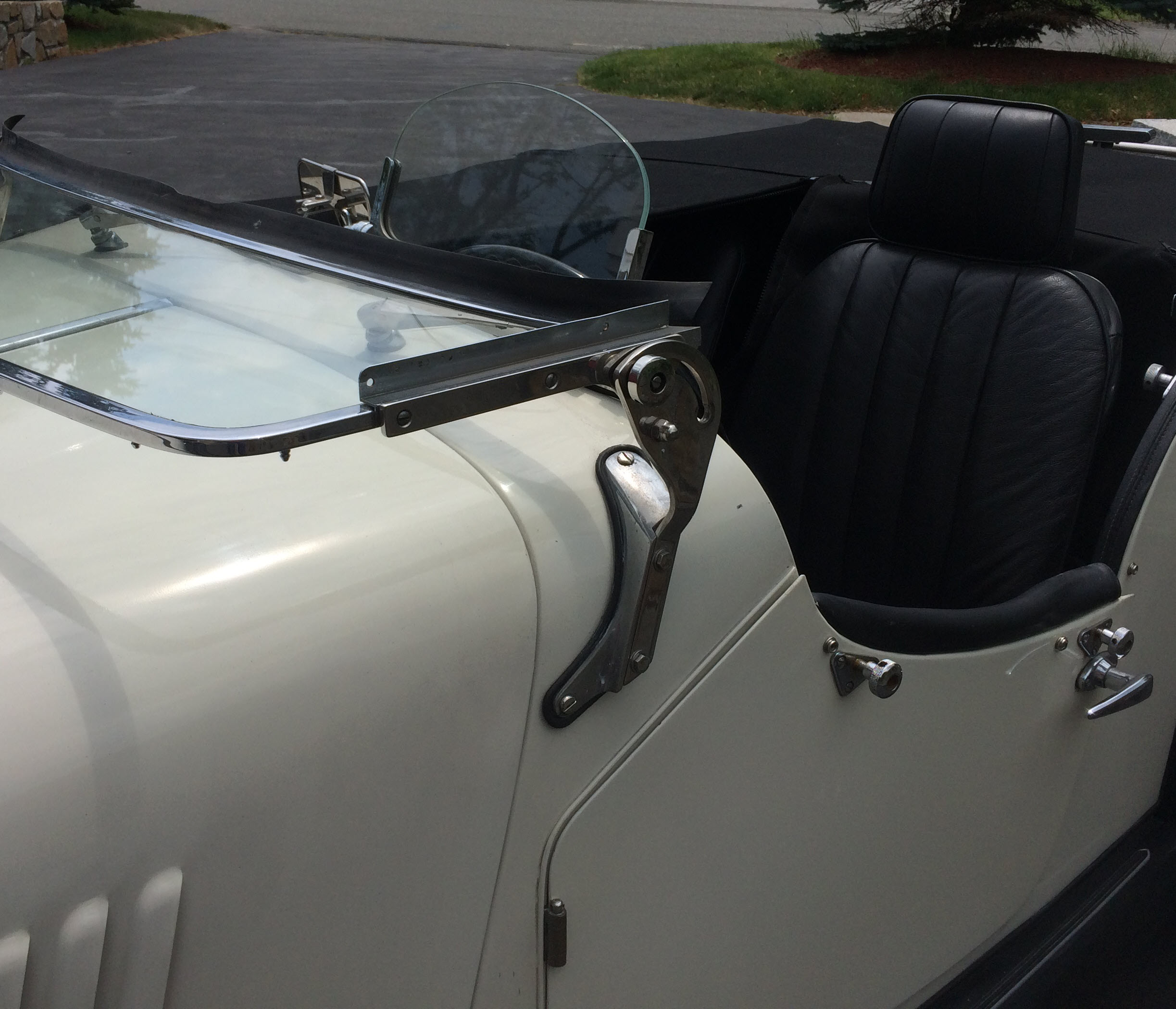
As Purchased from Morgan Spares via E-bay
Disassembly
Restore
Recondition clutch release parts (See additional information in the “How I do it” section.)
Rear Springs (See additional information in the “How I do it” section.)
Bumper Hangers (See additional information in the “How I do it” section.
Fabricating new wheel arches.
More disassembly required to complete wheel arches.
Wheel Arches continued.
Make “new shoes” for baby………….
Continue fitting wheel arches and make new sills.
Reconstruct Front Structure. bottoms of both pillars were rotted away as was top rail at hinge mount. Order of operations: cut top rail stock to accurate width and angle. Dado slots in each end for spline joint. Band-saw to profile. Dress the outside angle with a hand block plane. Pillars are similar: Square stock. Dado spline slot at end. Cross cut angle at bottom to match firewall/ chassis. Band saw outer profile. Dress angle with block plane.
Disassemble rear structure, glue and refasten original wood. Permanently attach to body tub.
Make new connecting blocks (attachment for hood bows, two cars). Fussy little part that is usually split and rotted. Order of operations: Route curved rabbet to match wheel arch. Table saw straight edges. Band saw (thin blade) curve to match hood bracket. Route rectangular recess for the elbow rail.
Lower rear cross piece. Order of operations: Dress stock to 1 1/2″. Rip to width. Hole saw radii of cutout. rip rear angle. Dado rabbet bottom rear edge and sides. band-saw remainder of cutout.
Fit and Assemble
Install connecting blocks. Mortise in wheel arch is cut using several passes with a plunge router following a cutout pattern in a piece of thin plywood. Same technique is used to make the rectangular recess in the block for the elbow rail.
Check fit parts
Anything you don’t explicitly make fit, won’t fit. Verifying that things fit and making corrections as you go exponentially increases the time it takes to complete anything. However; when you are done the odds are greater, (not absolute but greater) that the result is correct.
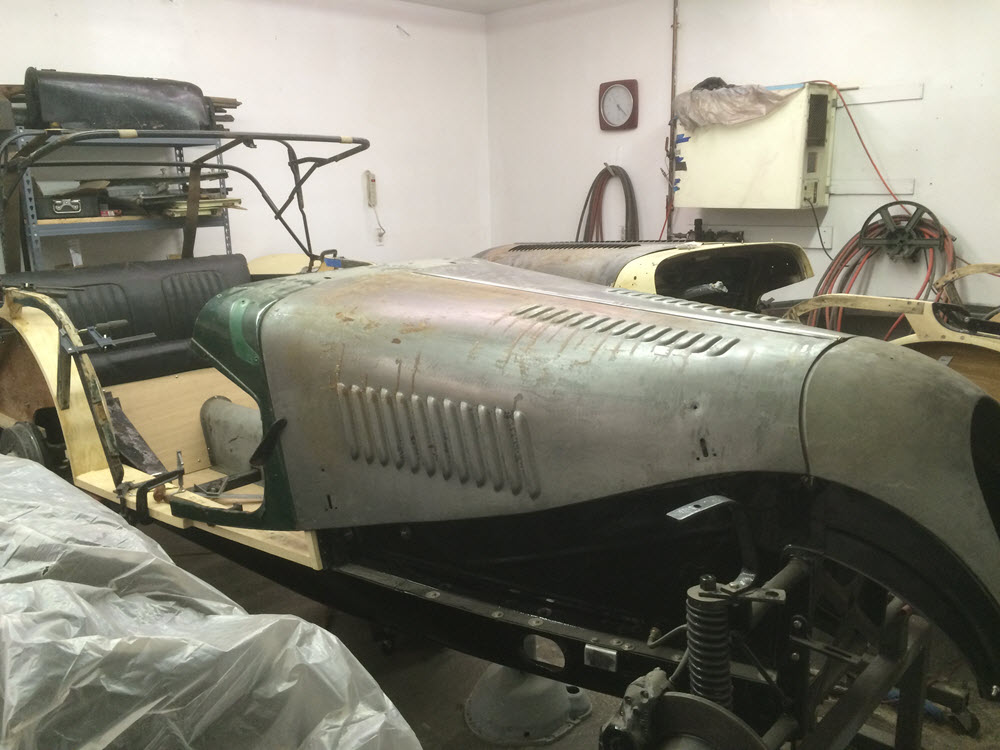
Make rockers (wood piece under door). The rockers are complex being shaped on all sides. For more information see: Building a Door Rocker in the How I do it section.
NOTE: I usually make patterns; the rest of the time I make scrap.
Make door hinge and striker posts.
Fit door hinge posts.
Make the door post knee rail. A very fussy part that sets the angle of the scuttle sheet metal. Close and accurate joints are essential. The order of operations: Cut the door post mortise on an oversize piece of ash, cut the forward end (compound) angle on the table saw then lower the blade and make multiple passes to make the inside rabbet. Check fit after each pass. The inside angle can be deceiving. One pass too many and the top of the door post won’t fit.
Cut the wing trim line on the sill and under the rocker. Note: The wing sits on top of the valence and then under the rocker. The cut on the rocker and sill must fair smoothly with the line of the valence top edge. Multiple passes with a router equipped with a guide bushing trim the rocker bottom and the sill to a depth of approximately 5/8″.
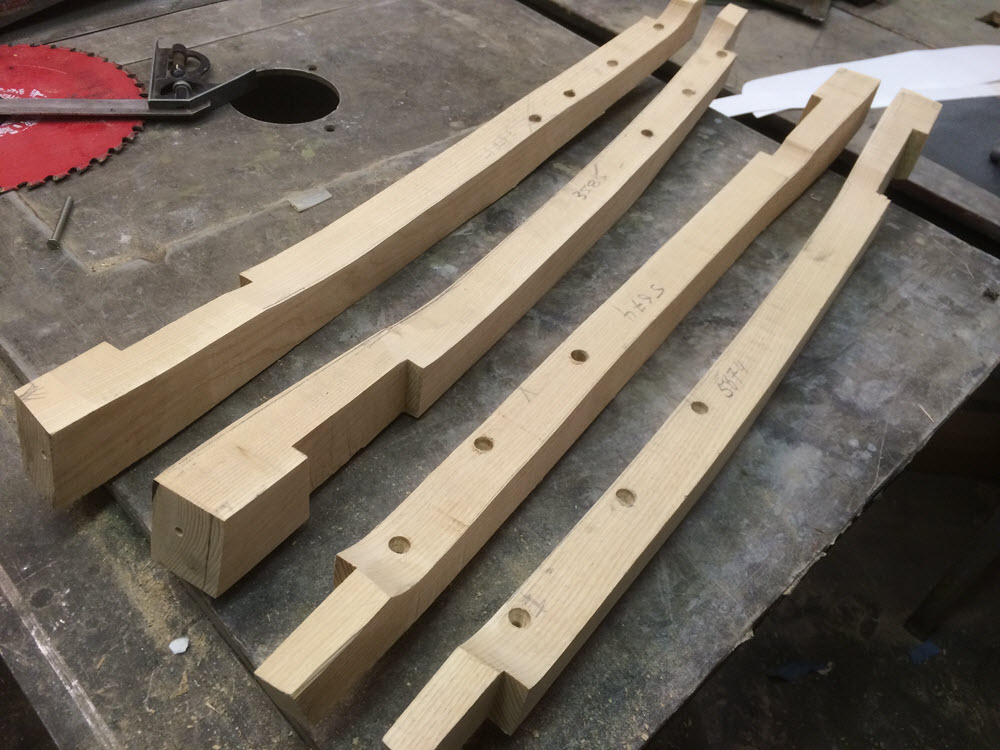
Cut the hinge mortises in the door posts. A simple fixture made of a 1″ thick piece of ash and 3/8″ plywood. the plywood is glued and nailed to the ash and then carefully cut on a table saw to make the two slots defining the hinge cutouts. the ash is clamped to the door post and the router makes the mortise in multiple full depth cuts.
Sheet Metal
Side Panels The first piece of sheet metal that has to be installed is the piece that begins midway under the door and ends over the wheel arch. It has tabs* on both the forward and aft edges that get covered by the adjacent panels. I rough cut the sheet metal, prep and prime the inside and lightly clamp it in place on the frame. Using a sharp awl I first scribe it all around on the inside of the panel to mark the fit on the frame. Next I use my homemade offset scribe to mark the trim line on the outside.
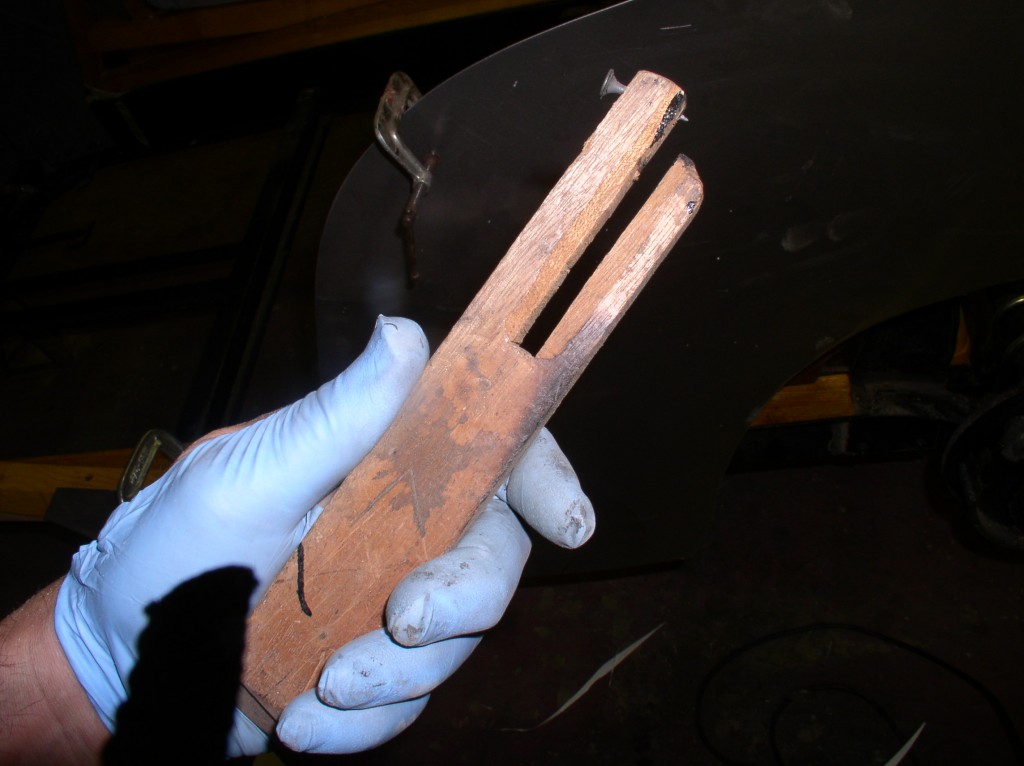
Pictured is the original tool that my granddad gave to my dad who in turn passed it on to me. The handle has be replaced several times and the nail has been upgraded to a drywall screw.
With the panel removed I cut to the trim line around the top edge only. It then gets clamped (lightly) on the frame with a piece of ash wood spanning fore and aft. The function of the wood piece is to minimize bouncing as the panel flange is hammered over the frame. Hammering the flange starts at the middle of the large curve at the top and works away in each direction. Light taps with the hammer on the flange start the bending while the non-hammer hand presses flat against the panel to provide resistance. The amount of pressure applied by the supporting hand determines the appearance of the finished panel. If pressed too hard the flange will be over-formed and the panel concave. Too little pressure and the panel will bulge. the ideal is not dead flat as that would appear hollow to the eye but rather very slightly convex.
* Tabs: Although not done by the factory and therefore not required, I make shallow mortises in the wood and recess the quarter panel tabs. I also tin them with lead tinning compound and lead the completed seam closed. My reasoning is that overlapping metal panels invite water ingress by capillary action if not direct flooding. Sealing the joint with something (I use lead but any goop will probably do the same thing) minimizes water entry. To keep the look of the overlapped panels I use a triangle file to cut a groove in the lead so it looks like a seam.
Scuttle: The piece that goes over the dashboard under the windshield is the only metal part of the body tub that I salvage. The bottom part on both sides, where it curves under the door and covers the rockers, is always rusted. I cut the bottoms off both sides at the upper hinge because I find it easier to replace entire lower pieces than to selectively fix the rust bits. The part is narrowest at the upper hinge so welding the new piece on is that much easier.
Rear Panels The factory used two separate pieces of sheet metal to wrap around the left and right rear corners. There is a seam where the two panels join at the bottom center of the spare tire cutout. In a previous four-seater project from ages ago I had a problem making the transition across the panels look right. I don’t remember what the problem was but ever since I’ve been making the entire rear out of a single piece of sheet metal. Using a single piece eliminates the panel matching problem but is very wasteful (almost an entire sheet is required for one car) and is cumbersome to handle. The spare tire rolled wire edge is done first then the whole bit is clamped in place on the rear of the car. The actual bending of the panel around the body is done by hand. This is not an easy bend to get right. hand bending sheet metal is a bit like managing a teenager. As long as you allow absolutely no other options, it will always do what you want.
Doors
the following is an attempt to describe how I make a one-off door frame from scratch. It is certainly not the way the factory does it.
Making the Door Wood Framing: If the joints of the wood have any rot it is better to replace it rather than attempt a repair. Thick epoxy and similar fillers are short-term solutions at best. Scarfing (joining new wood to old by cutting a 7-to-1 or greater angle glue joint) takes almost as much effort as making new parts. Scarfing is a good solution if only one side of the joint needs replacing. On this car several joints were bad on each door so I made new doors from scratch.
Before going to much further some observations are in order: 1. The thickness of the door hinge piece (A) is greater than the thickness of the door post in the body. This is not an accident. The difference in thickness provides the offset required for the door sheet metal to overlap the body sheet metal when the hinges are installed correctly. 2. Viewed from the side the piece of wood that forms the bottom of the door frame (B) is perpendicular to the front (A) hinge piece. 3. When viewed from the front, the hinge piece (A) of the door frame leans in at the top while the rear (C) piece is vertical. 4. The top-front piece (D) is coplanar with the hinge piece (A). 5.Good joints equal a good door. If the five joints are done well the wood separating them can be shaped as required to fit the body.
The process I have evolved may not be the most economical but all but two of the joints are simple. The lower front (A to B) is a compound angle as is the top most corner (E to D). These are fiddly and take care to get right. OK, depending on the particular car the top rear joint (E to C) may need some extra dressing also.
Starting with rough stock milled to 1 1/8″ thick I make the hinge recesses in the front door posts (A). After tracing a pattern the top and bottom ends are trimmed to fit the opening. With a dado set in the table saw the halving joint for the bottom (B) is cut perpendicular. Using an angle gauge, the angle between A and D is determined and the halving joint cut with the dado set. Install the hinges and fit A into the car.
Make part D. Because it is coplanar the joint is a simple halving cut at the correct angle. Clamp D to A in the car.
Make a paper pattern of part C. To get the correct angle for the joint with the bottom piece (B) clamp a straight piece of 1″ square ash in the bottom joint of A.

Several paragraphs were accidently deleted. I will redo them soon.
to be continued:
Engine Stuff I’m not an engine guy, really don’t particularly like putting engines together, but I have had to build a lot of TRs, Ford Kents, Matchless and JAPs over the years. The TR is unique despite it reputation as an agricultural version of a boat anchor. The designers took pains to make it repairable by part replacement rather than reliance on sophisticated machine shop availability. If your +4 throws a rod in Timbuktu you can have Uncle Melvyn send you new bearings, a rod and even a new wet sleeve and with a Koyra Chiini translation ap on your phone plus a few basic spanners, the local Imam will have you back on the road again in no time.
Taking It Apart The engine in 5674 had been previously rebuilt by someone who was not familiar with the TR engine. How can I tell? See below.
Prying the front cam bearing and the rear main bearing cap does not work. Pipe wrenches and vice grips should not be used to remove studs.
Wrong (too long) screw pushed through the front alloy block.
It takes but a few minutes to make a tool from some ash scraps and 5/16″-18 threaded rod to properly withdraw the front and rear main bearing caps. A similar tool will pull the cam to withdraw the front bearing. Studs can be installed or removed without damage by tightening two nuts on the end and turning with opposing pressure on a pair of wrenches. The only way to make sure a screw fits a hole is to check fit it without the mating part. Holes collect crud and even boiling does not always get it out. Chasing the holes, that is cleaning them by loosely threading a tap in, is a particularly good idea if the engine has be previously “rebuilt”. If a proper tap is not available a few hack-saw cuts across the threads of an old stud will make a reasonable facsimile.
Head studs and nuts There was a time when I was stripping the head nuts rather regularly when tightening to the specified torque. I assumed that the nuts failed because they were being reused or were poorly made reproductions. I sourced and used Grade 10 full nuts and even then I managed to strip one or two with every assembly. Finally I did some research and found that the 100+ foot pounds torque was specified for “clean and dry” nuts and studs. I typically oiled or applied Loctite to the threads. Bad idea. Since I stopped lubricating the nuts I have not had any problems. “Clean and Dry”; keep it in mind.
Remove and Replace Cam Bearings. Expect low oil pressure if you do not replace the cam bearings. I have a simple tool for removing and replacing cam bearings. It consists of a length of 1/2″-13 threaded rod, a block of wood to center the rod in the front cam bearing hole, and a stepped piece of aluminum to support the bearing.
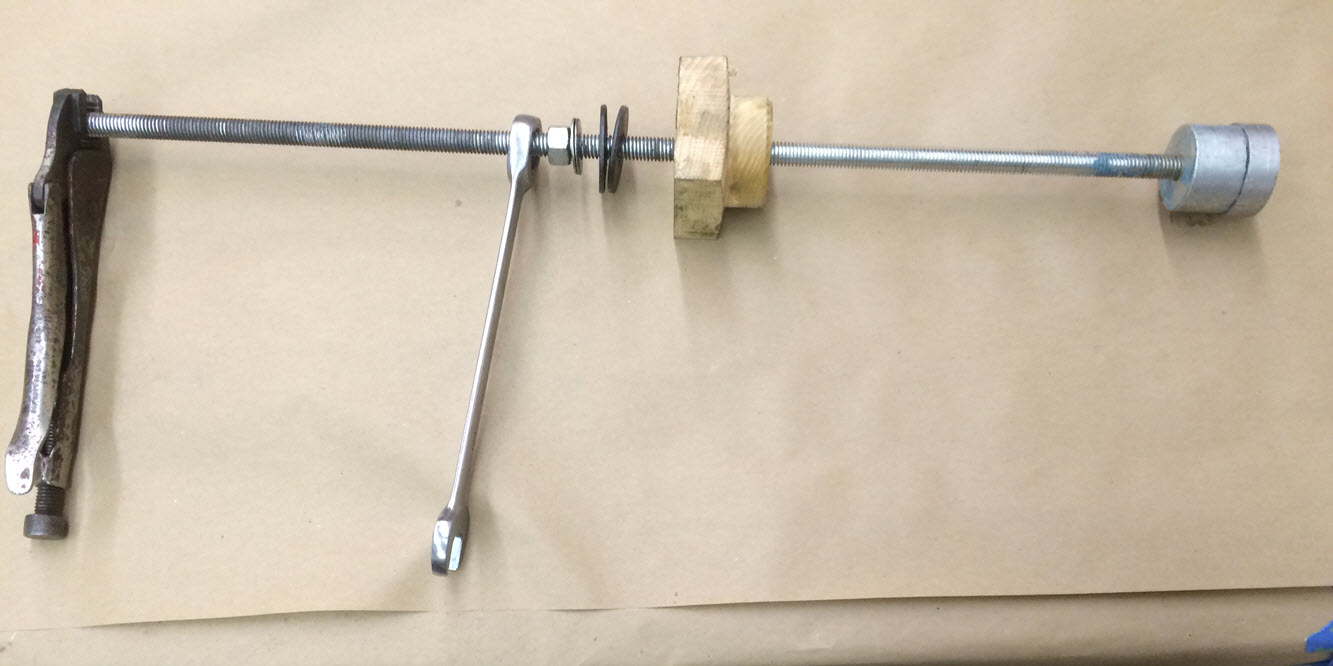
The support has a minor diameter that is a slip fit inside the bearing and a major diameter that is a slip fit in the hole where the bearing fits. It is tapped full length for the 12″-13 rod. Installed in the block as shown a vice grip prevents the rod from turning while a ratchet wrench tightens a nut to pull an old bearing out or a new bearing in. I do the rear most bearing first and then tip the block on end to do the next two. Note: everything gets liberally coated with assembly oil before and during installation.
The hardest part of installing cam bearings is correctly lining up the holes in the bearing with the holes in the block where the dog-point set screws fit. Any interference between the dog-point and the bearing will push the bearing against the cam. In the worst case the cam will not turn at all. Always put the cam wheel on loosely and rotate the cam by hand to verify that there is no resistance to turning. There is a file mark on my stepped aluminum bearing support to line up with the hole in the bearing and then with the hole in the block before pulling it into place. If the holes do not line up perfectly, it is not a big deal to continue pulling the new bearing all the way through to start over.
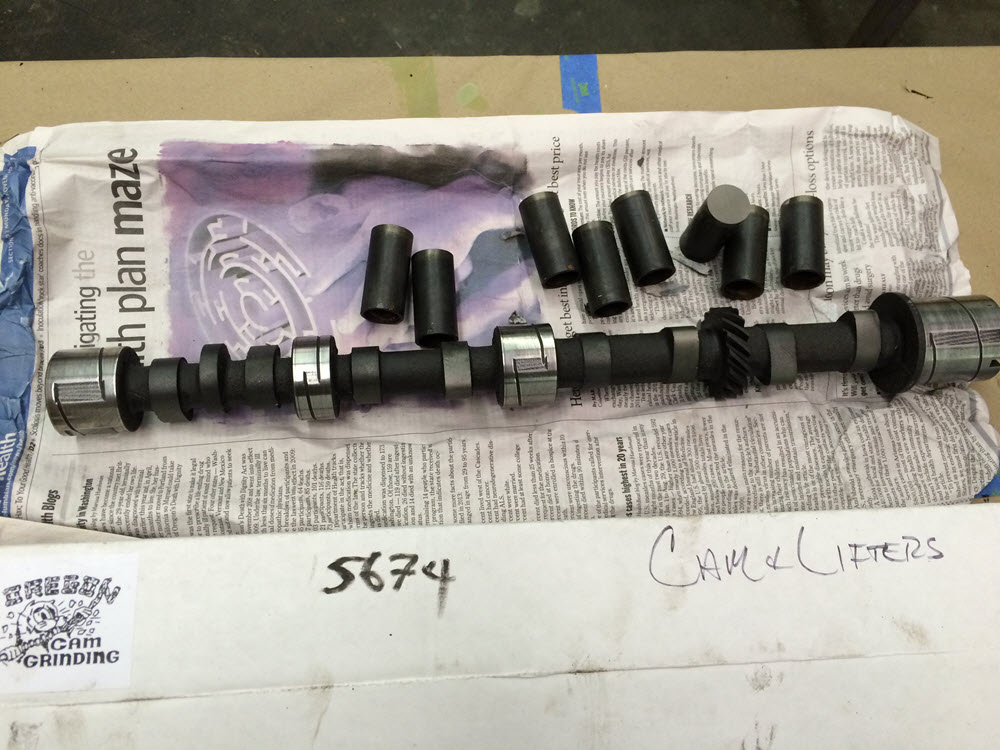
from Oregon Cam Grinders. Stock grind
Install new Wet Liners. On the 1967 DHC project I chose to simply hone the existing liners, rotate them 90 degrees and reinstall with new rings. I could do that because the engine had never been apart and the wear was within acceptable specifications. This engine was previously buggered leaving no choice but to either rebore or buy new piston/liner set. I chose the new set. Before installing I soda blasted the block inside and out, treated it with OSPHO conversion coating, brushed etching prime on the exterior and the interior wet area and finally brushed Imron on the interior wet area.
A high quality sealant is brushed under and over the figure 8 gaskets. I have two homemade retainers to prevent the liners from shifting during the installation of the pistons. To make the retainers I cut an old stud (or maybe a long bolt with the right thread, it was a long time ago so I’m not certain) drilled the cut end and brazed in a length of 5/16″ threaded rod. A segment of a large diameter washer completes the retainer and bears on the top of two adjacent liners.
Front Mounting Plate Any TR engine with enough miles on it to warrant rebuild will have a significant groove worn into the front mounting plate, under the timing chain tension spring. Ages ago I tried filling the groove with weld using Oxy/Acetylene. It was a disaster. Front mounting plates are unique for Morgans, Warp or otherwise make one unusable and it is not easy to find another so after that one bad experience I played very conservative for thirty years and just ground the sharp edges of the groove and put it all back together. The groove on this engine was more than halfway through the plate so I revisited the welding option. This time I used MIG and it worked beautifully. The plate was firmly clamped to the iron base of my table saw for support and heat sinking. It worked so well in fact, that I also welded the depression and elongated hole at the generator mount.
Rotating and Reciprocating Parts I’m not a racer or performance nut. If I wanted a car that had the power and performance of a modern sports car I would buy a modern sports car. I drive old Morgans and, with a few exceptions, I am content with rebuilding them to the original standard. Balancing is one of those things that I always did when I could pass the charge on to a customer but for my own cars I usually left things as original. The plans for this car (5674) include some long distance touring far from home so I’m using a belt and suspenders approach that includes replacing many parts that were simply marginal and also a complete balancing of the rotating and reciprocating parts. Everything that goes round and round was sent to Lindskog Balancing in Boxborough MA.
Rear Main Seal If the engine leaks through the rear main it is because something else is wrong. The seal is a labyrinth design that has no contact so it will never wear a groove in the crankshaft. Converting to one of the “new and improved” lip seal options is an expensive step backwards. The factory workshop manual describes using a special mandrel to center the seal. I don’t have one. It was after I completed this job that I noticed that they are available through Moss Motors. Even though I swear this is my last Morgan I would have bought a mandrel had I known. My alternative process: 1. install the main shell bearings in the block, 2. apply gasket sealer on the mounting faces of the seal halves and loosely fasten them to the block and bearing cap. 3. Oil the shell bearings. 4. Place the crankshaft in the block. 5. insert the shell bearing in the rear main cap. 6. Assemble and torque the rear main cap. 7. Rotate the crank by hand to verify fit. 8. With a small drift, lightly tap the seal halves together around the crankshaft. 9. Use a torque wrench to tighten the seal fasteners. 10. Continue with assembly.
Packing the rear bearing cap is a rather bizarre operation if you think about it. The manual says to cut the felt strips into shorter bits, soak them is gasket goo, and pack them in the hole with a drift. If that is what the manufacturer says to do; that is what I do. The people that designed and built the engine are smarter than I am. It is just that I cannot imagine this being done in production on the assembly line when the engine was originally built. “What’s your job mate? I pack the wad-o-wool…”
Also; if you follow the manual instructions the strip of felt that comes in the rebuild kit will not be enough. I have blocks of felt that I use to make hub seals for trikes and cut extra strips from that. Any cotton rag will probably work as well provided ample gasket cement is used.
Ages ago I remember John Sheally recommended trimming the sides of the rear seal flush with the sides of the bearing cap. The stock design, with the seal overlapping the bearing cap makes it impossible to withdraw the cap with the flywheel attached. In other words, the engine must come out to service the main bearings. When assembling engines for customers thirty years ago I would trim the seals. Seems silly now. If I have a bearing failure I want the engine out, pure and simple. No trimmed seals thank you.
Front sealing block. I destroyed more than a few T shaped cork gaskets in my time. Finally I learned to trim them to be a snug fit in the end recesses of the aluminum block, apply gasket goo, and use a thin feeler gauge on one side to compress and slide them into the block. The factory manual says to align the front of the alloy piece with the front face of the block. What the manual does not tell you is that the location of the alloy block is dependent on the location of the front main bearing cap. Be certain to align the front main bearing cap with the front face of the block or the alloy block won’t.
Oil Pump Way back in 1973 my daily driver ’53 +4 had extremely low oil pressure. I rebuilt the Vanguard engine (my first experience with the TR family of engines) and it still had virtually no oil pressure. I suspected the oil pump. To test the pump I flattened the end of a long steel rod, removed the distributor tower and inserted the rod down the hole until I could feel the flattened end engage in the oil pump. With an electric drill I spun the rod. Nothing happened. Ah! the pump must be bad. Then I reversed the drill. Believe me these pumps can really move oil. Try the experiment yourself sometime but be sure you are wearing disposable clothes. Eventually, after the second rebuild, I found that the pressure relief spring in the oil filter body was broken.
The factory manual gives maximum clearances for the rotor and end float. Complete new pumps or new rotor sets are available. In my experience, even old worn pumps work fine, however, I recently replaced the rotor set on another engine and observed the hot idle pressure jump from near zero to about 20psi. I typically lap the pump end cap to remove the wear grooves. 220 wet-or-dry sandpaper on a flat steel surface works fine. If you are reusing the old rotor set the same technique can be used on the body of pump to correct excessive end float . For this engine I bought a new rotor set because it was fairly cheap and the old rotor was pretty bad. Lastly; always stick a screwdriver down the pump end and make sure it turns before you install it in the engine.
Pretty Stuff Now this is really silly. I ground the exhaust manifold smooth and sent it to Jet-Hot for ceramic coating. Yes, there are people that say the ceramic reduces the heat and has all sorts of benefits but for me, it was just aesthetics. Rust is the correct finish and if I were a concours judge (NEVER!) I would take off points for anything other than rust on an exhaust manifold.
Transmission It is not my cup-o-tea but I will do engine work if necessary. Years ago I decided I did not want to work or gearboxes and differentials. I took the Moss gearbox for this car to John Esposito at Quantum Mechanics in Oxford, CT. A quick look with the top off the gearbox was encouraging. All the gears looked good so the plan was to replace all the bearings and seals. Reality hit when the gearbox was disassembled. Both the main and layshafts were worn and had to be replaced.
Radiator A 50 year old radiator is not something I want to trust. I always re-core using, whenever possible, the original top and bottom tanks. The trend today is toward aluminum radiators. Copper transfers heat more efficiently than aluminum so unless weight is an issue I will use a copper replacement core. The top tank on this car looks like it was used to stop forward motion at one time. After removing the tanks, examine them closely. It is not unusual to find hair-line cracks.
OK; the top tank could not be salvaged. I made a new brass top tank and repaired the bottom tank. The top tank follows the earlier pattern and is silver-soldered together. Generous seam overlap, cleanliness, and careful heat control are the key to making a strong tank. Propane won’t do. Oxy-acetylene is best and there is a fine line between flowing silver-solder and a hole where the brass used to be.
The above pictures are from a different car but the process is the same. I like to have an electric fan as a back-up. The engine ‘should not overheat but… An efficient installation would require a shroud but since I only hope to use this fan when climbing the alps I did not bother. Fan kits mount the fan directly on the front face of the radiator. Not only is that an inefficient installation, it is noisy. I prefer to have the fan an inch or so off the face of the radiator. A little space improves the pressure distribution and eliminates the wind-shearing noise.
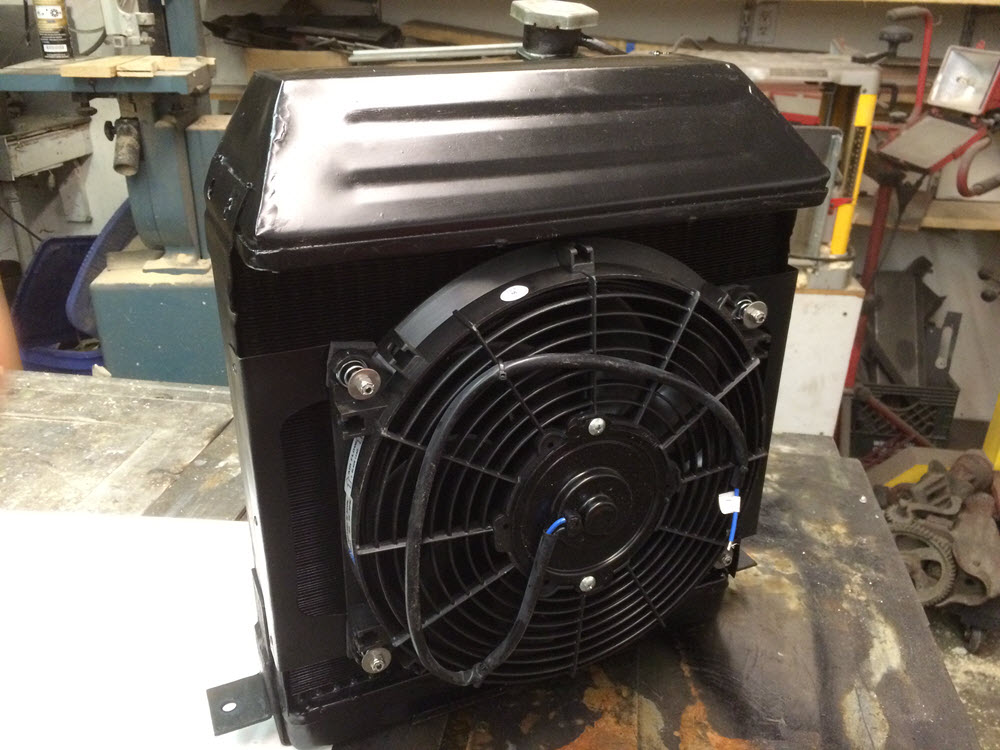
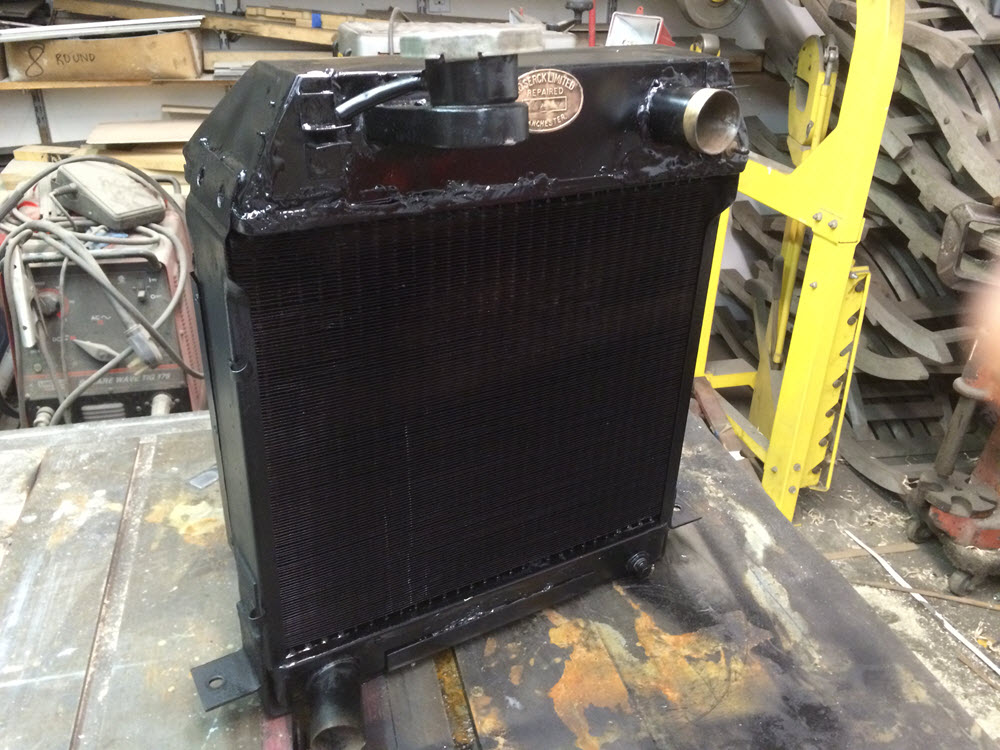