Oh my gosh; I wrote this in 2015 before our first trip to Europe. It is now 2025 and BENE has been back and forth across the Atlantic eight times and got stuck in Italy long enough to earn citizenship (the Covid years). The experiences gained from each tour motivated many new changes. Additional text will be in Italics and the new photos are captioned.
I acquired my 1967 +4 DHC from Morgan West in 2009. It was not the top priority in the shop and so was not completed until 2014 when it was sent back to California for Barbara Willburn to make the top and attend Mog West. My vision for the car was that it would be used for touring and towing my three wheeler on a trailer. Reliability was the overriding concern. Since that first California tour it has taken us on many outings including a 1000 mile round trip to Gettysburg for the DC group’s MOG 45. All in all it is certainly not perfect but has performed well. This year Kathi and I decided we wanted to visit Italy. One of my current projects is a 1964 +4 four seater. This was to be the “Italian Job” but the DHC has behaved so well that the four-seater got bumped and I am waiting for the truck to collect the DHC as I type this.
I took some liberties (yes, heresy) with originality building the car and again in preparing it for the Italian adventure. Mechanically the only change was a gear reduction starter but the following documents some of the other changes. Time will tell what works and what doesn’t.
SEATING:
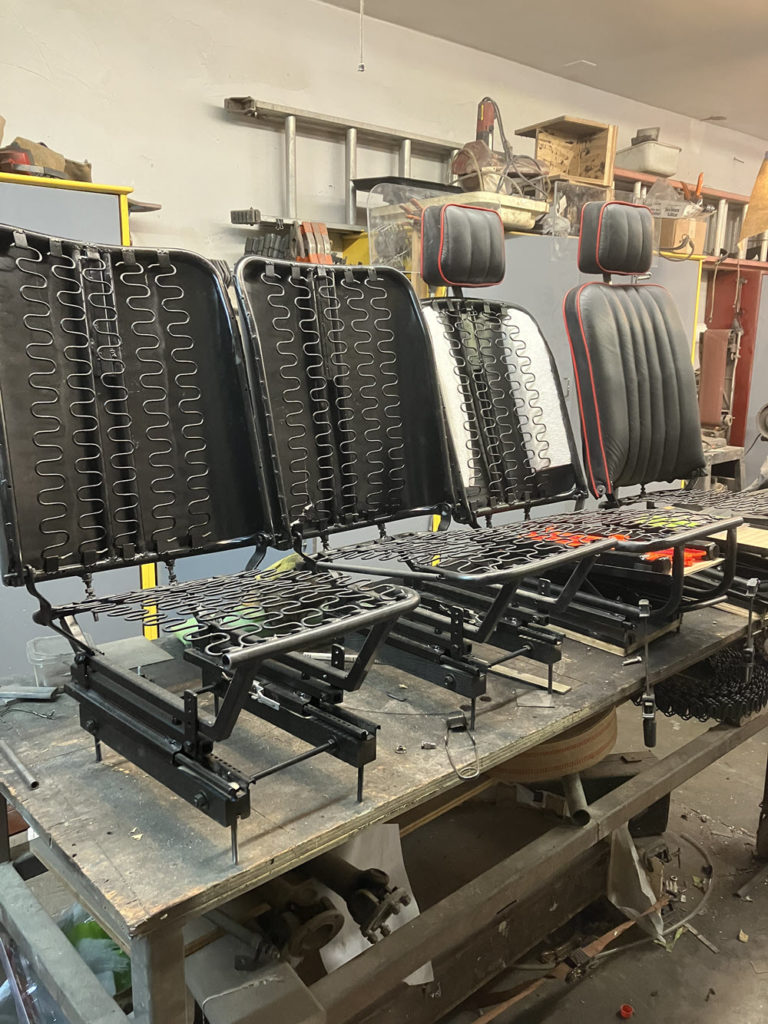
The adjustable seats worked fine but even with foam stuffed under them they just did not have the support I need for long hauls. I changed to upholstery type springs, added headrests and for 2023 tour added acrylic wind shieds behind the headrests. I added a description of the seat mods to this website under the “How I Do It…” heading.
I’ve had multiple back injuries so standard 1960s era Morgan seating won’t do for extended periods. Also my wife, Kathi, drives the car so the seats need to accommodate both of us. Early in the restoration I had Barbara Willburn make standard bench seat upholstery. At the time I was not planning on keeping the car as dropheads were not my cup-o-tea. As time went on and my attitude changed I tried to make an adjustable version of the bench seat. It was an engineer’s worst nightmare: it looked great on the computer, worked terrific when bolted to the workbench and did not work at all in the car. I used it as a fixed seat until the decision to send the car abroad. On previous four-seat project cars I’ve used sliding tracks from other British cars that I purchased through Moss Motors. They worked to a degree but were not super. Recently I purchased universal track assemblies made by Sparco and installed them in the two four seaters currently in the shop. I was very happy with the results so it seemed like ‘a good idea at the time’ to put the four-seater sliding seats into the DHC. That too worked great (but now I have to make new seats for the four-seater). Because the Sparco seat slide worked so well I made additional modifications to the seats for comfort. I should mention that all four-seater front seats that I have ever worked on have bent and distorted lower back rails. It is just a design flaw that the factory never bothered to fix. I either straighten or replace the bent part and then reinforce the back by welding a 3/16″ X 3/4″ piece of steel (later examples used tubing) top to bottom on each side of seat back. The reinforcement also provides a mounting point for my home-made seat belt shoulder guide. The driver’s side seat needs the most travel so I also made a replacement support on the seat bottom frame to clear the rear spring cover.
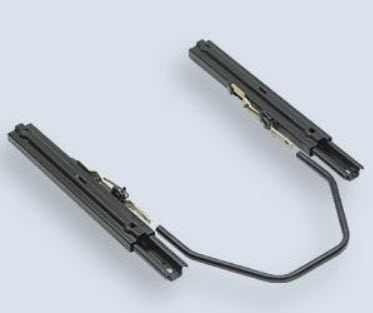
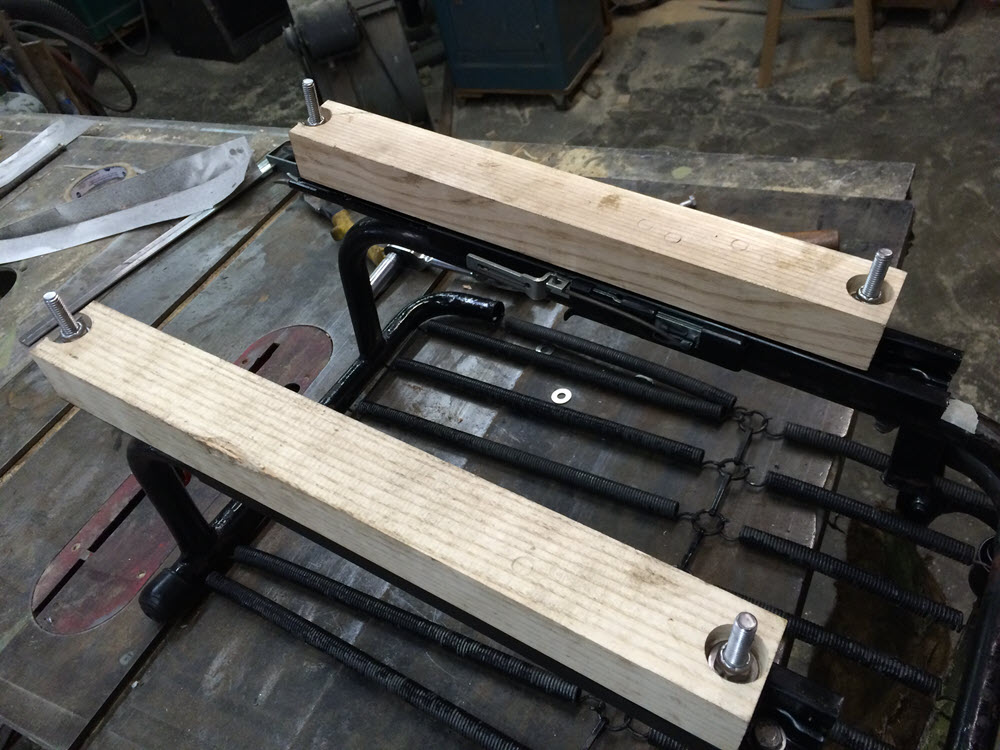
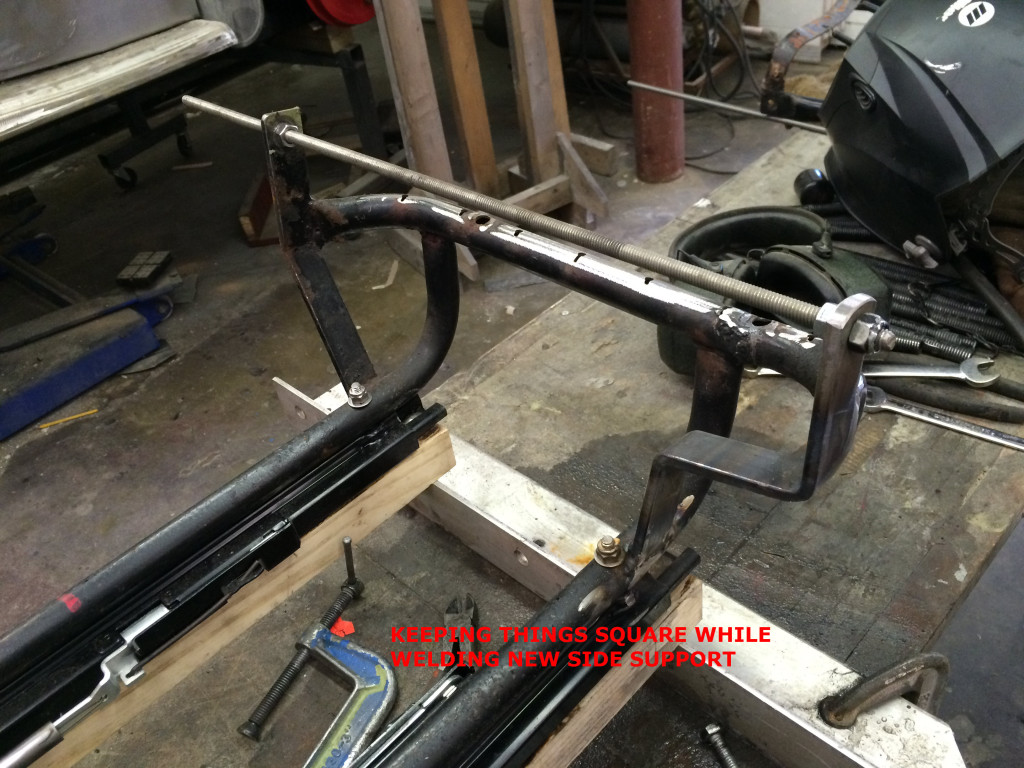
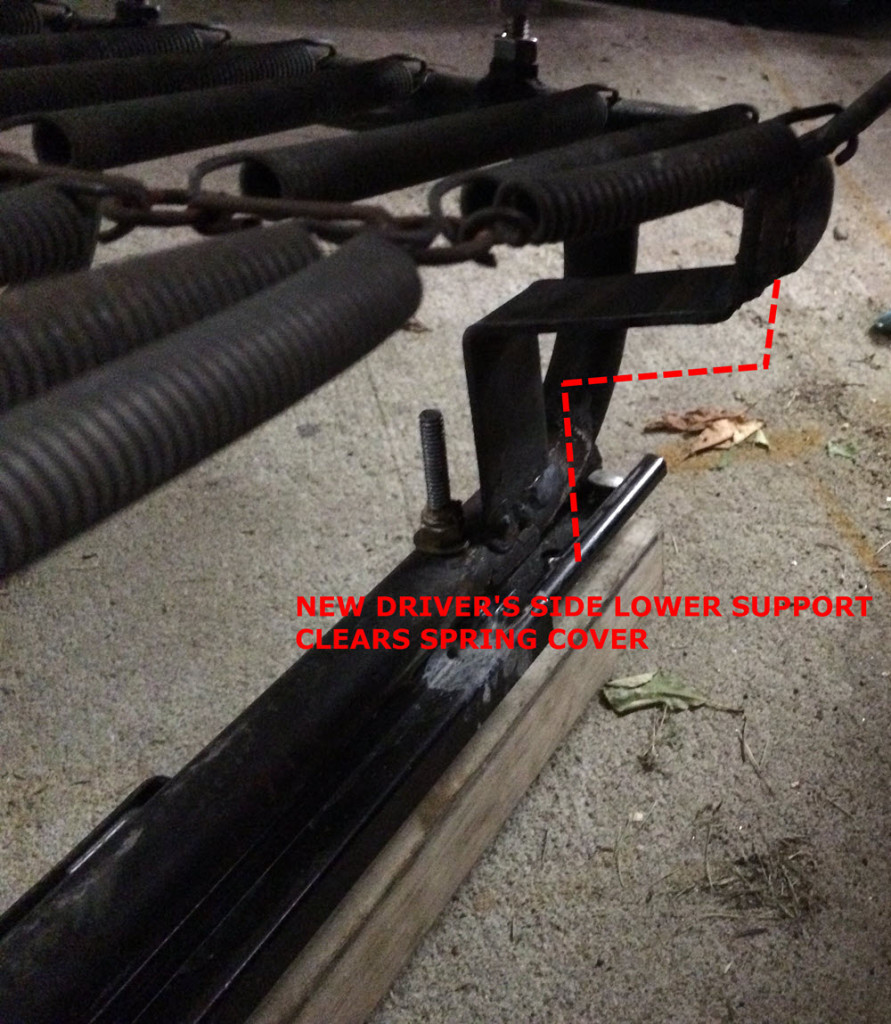
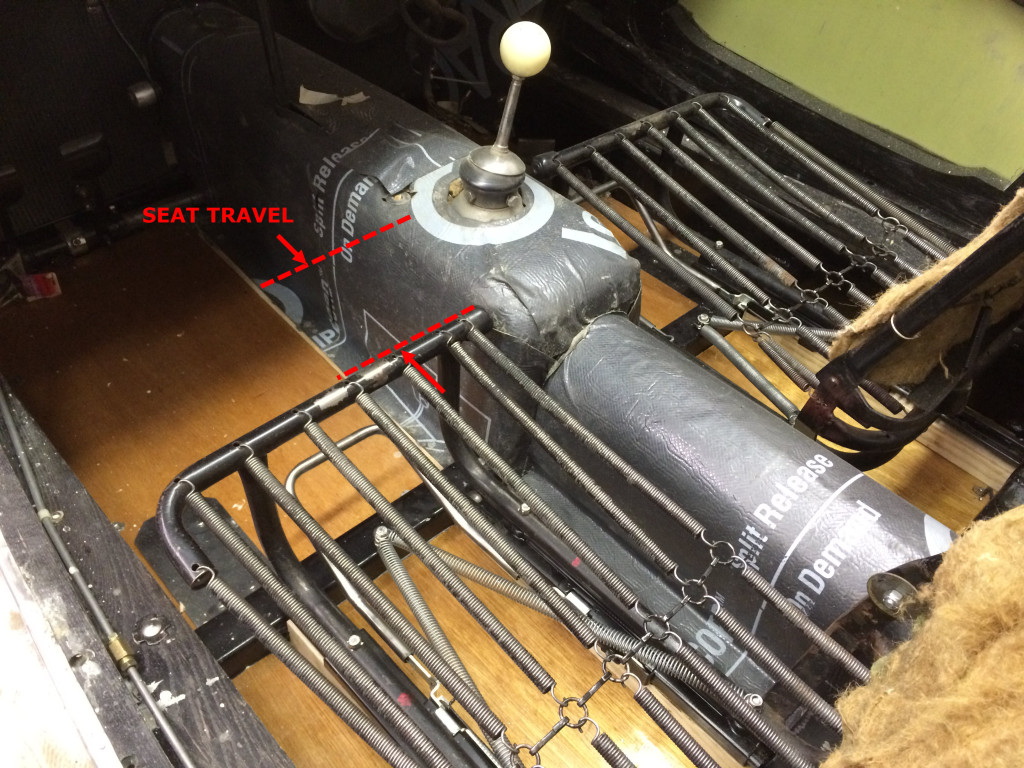
All that worked well so I continued fiddling. I made a sheet metal cover over the entire rear of the seat back. That allowed me to insert 1″ thick foam behind the stock coil springs for better support. When that change worked as planned I welded a piece of angle iron on the front and rear tubes of the seat bottom frame 2″ below the coil springs. A plywood platform completes the structure and supports two layers of 1″ foam. After driving with this set-up for a while I think it is a good compromise. The stock springs alone deflect too much initially whereas just solid foam compresses and becomes rock like. As installed the foam compresses but resilience is maintained by the springs. Check out the pics. Of course the final upgrade of replacing the factory spring set up with conventional upholstery spring made all this obsolete. See top picture.
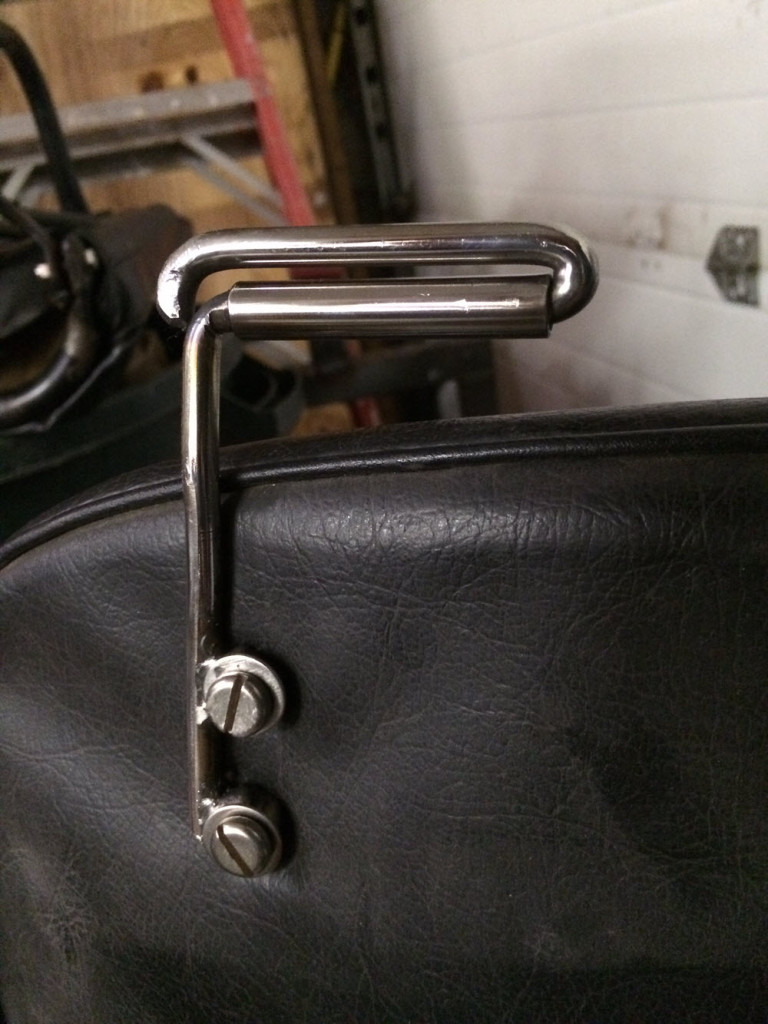
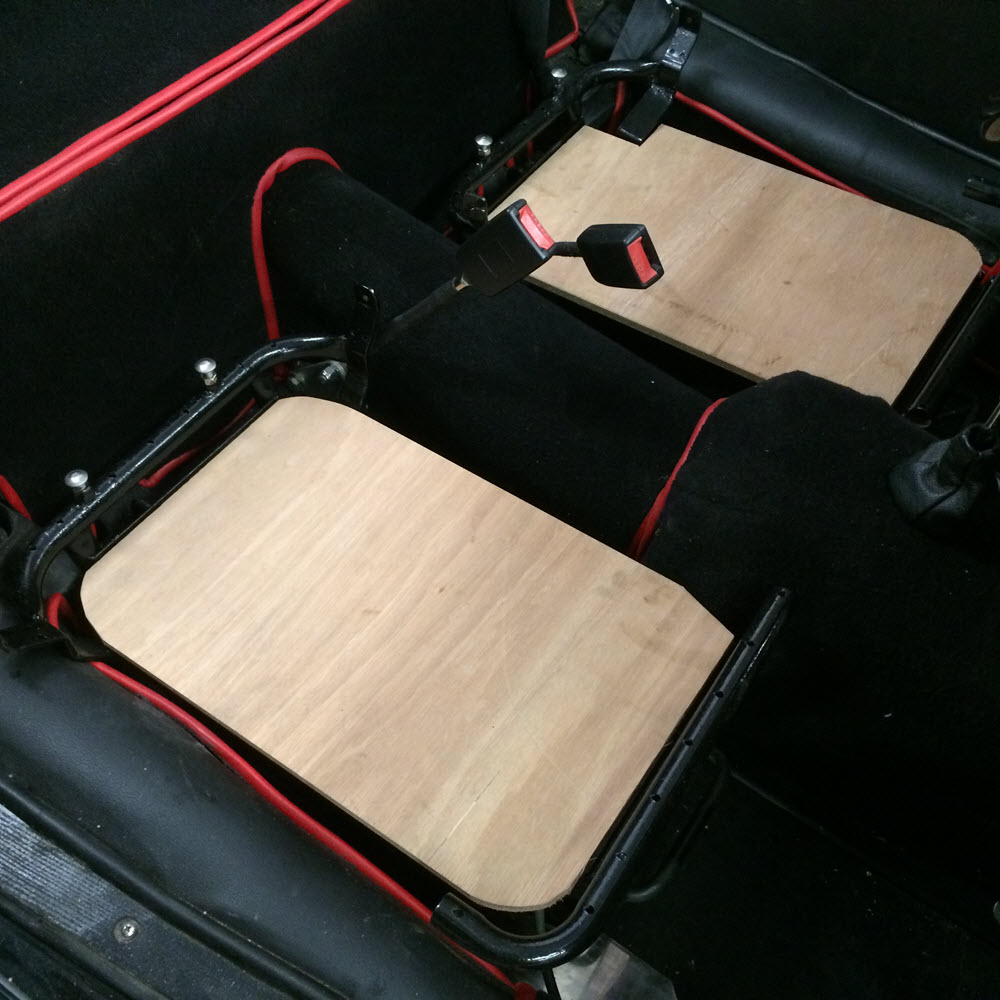
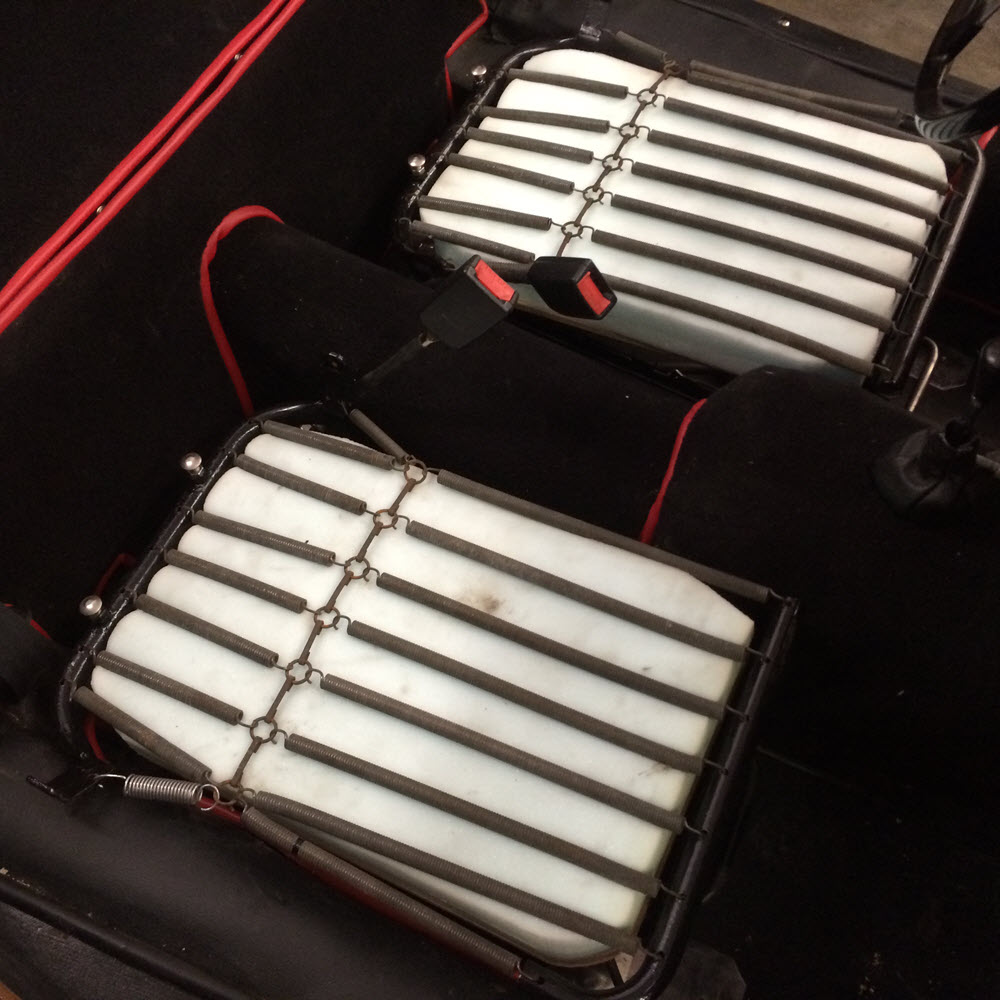
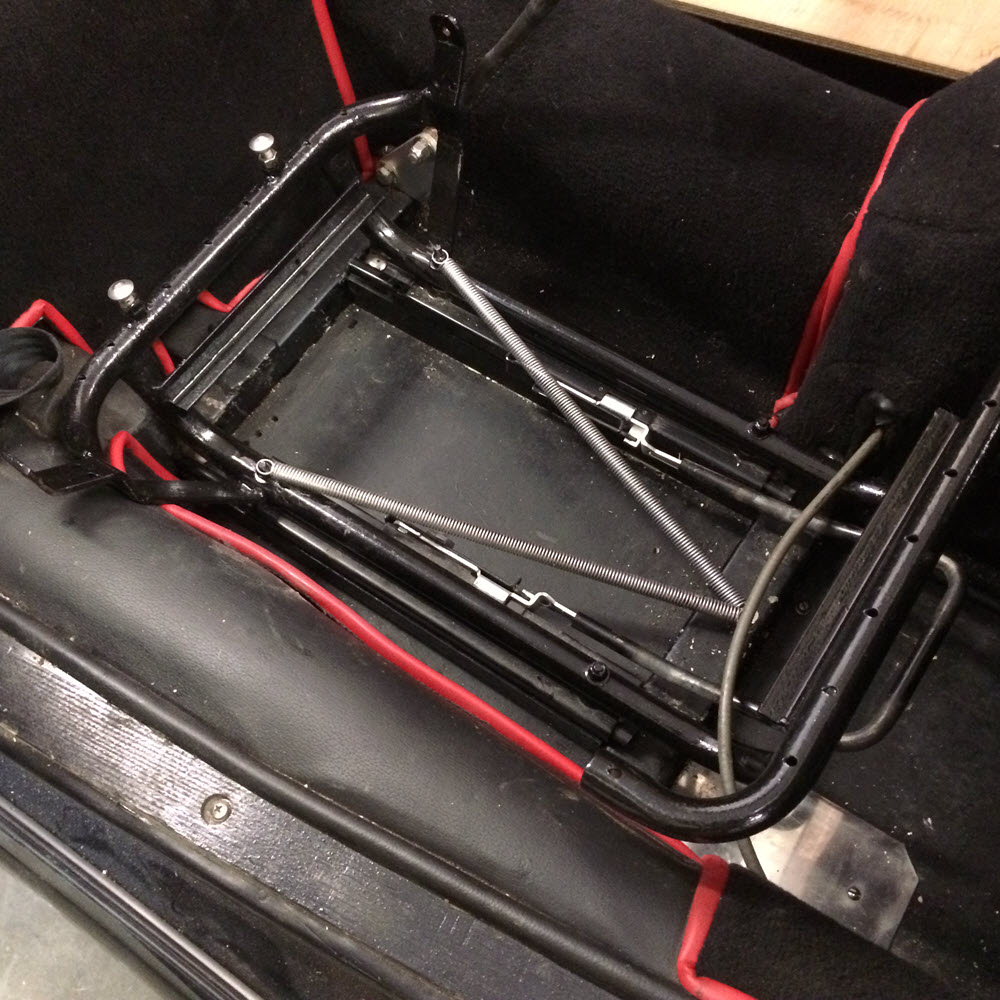
TOOLS:
On two different trips with the DHC I got flat tires. Aside from dealing with a crappy jack it was not a problem to change wheels. I did learn to carry a spare tube because those are not available at every gas station. I made an ash shelf behind the spare (DHC has a high gas tank) in the same place that the gas tank support shelf would be on a roadster. To this I clamped a large scissors jack, knock off hammer, crank and block of ash to hammer against the knock offs. A 1/8″ thick aluminum disc fits inside the rim of the spare wheel hiding everything.
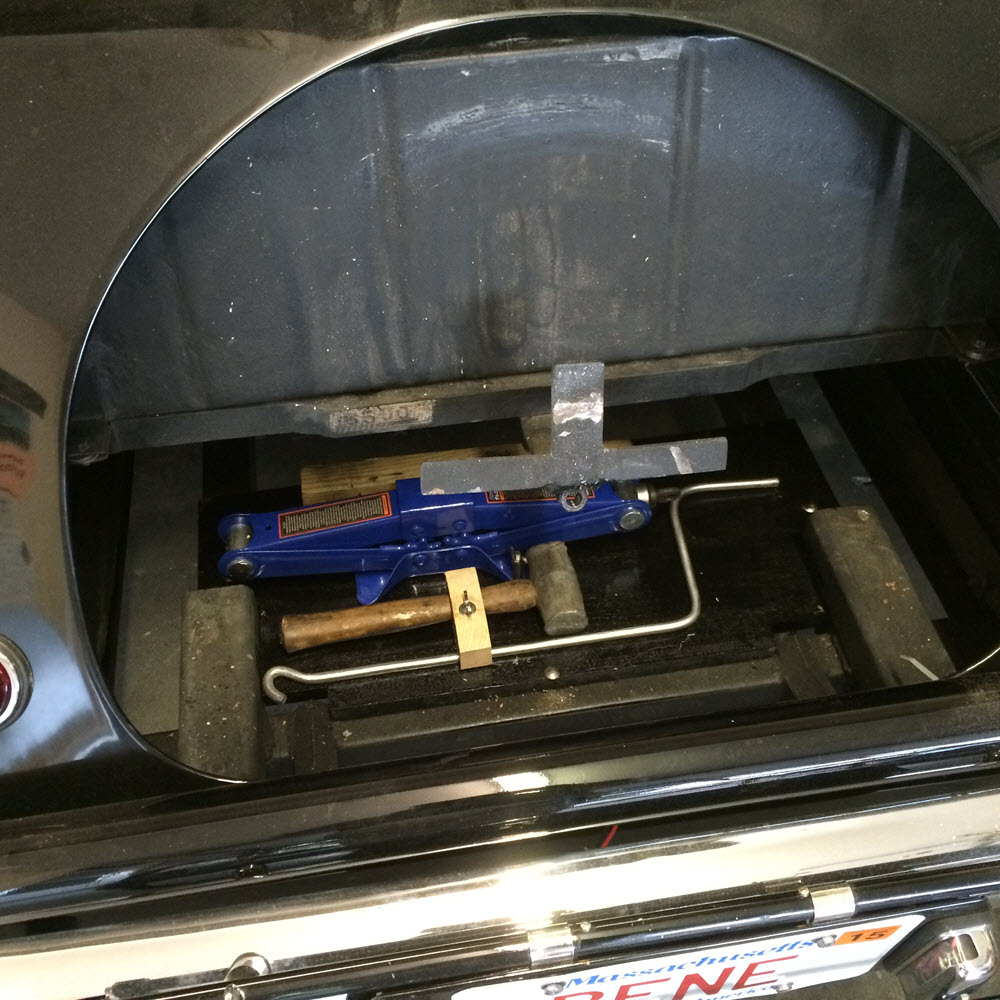
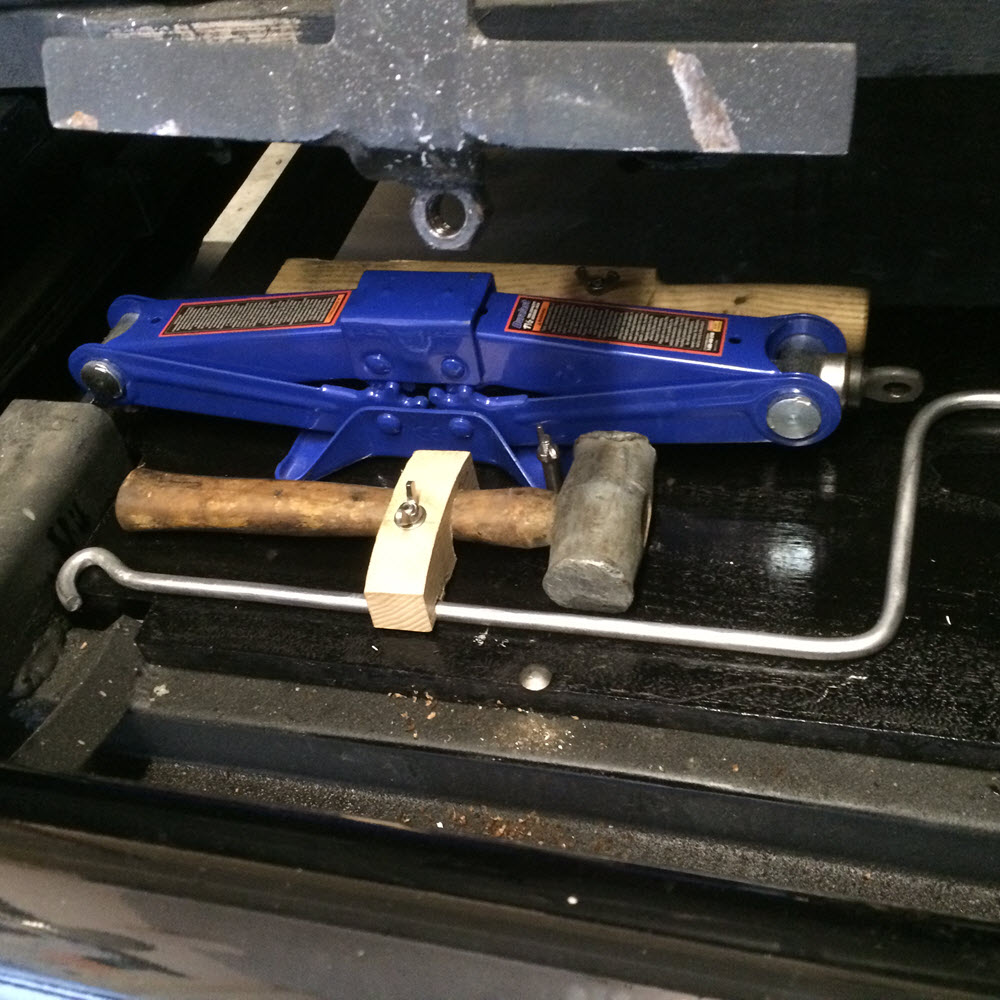
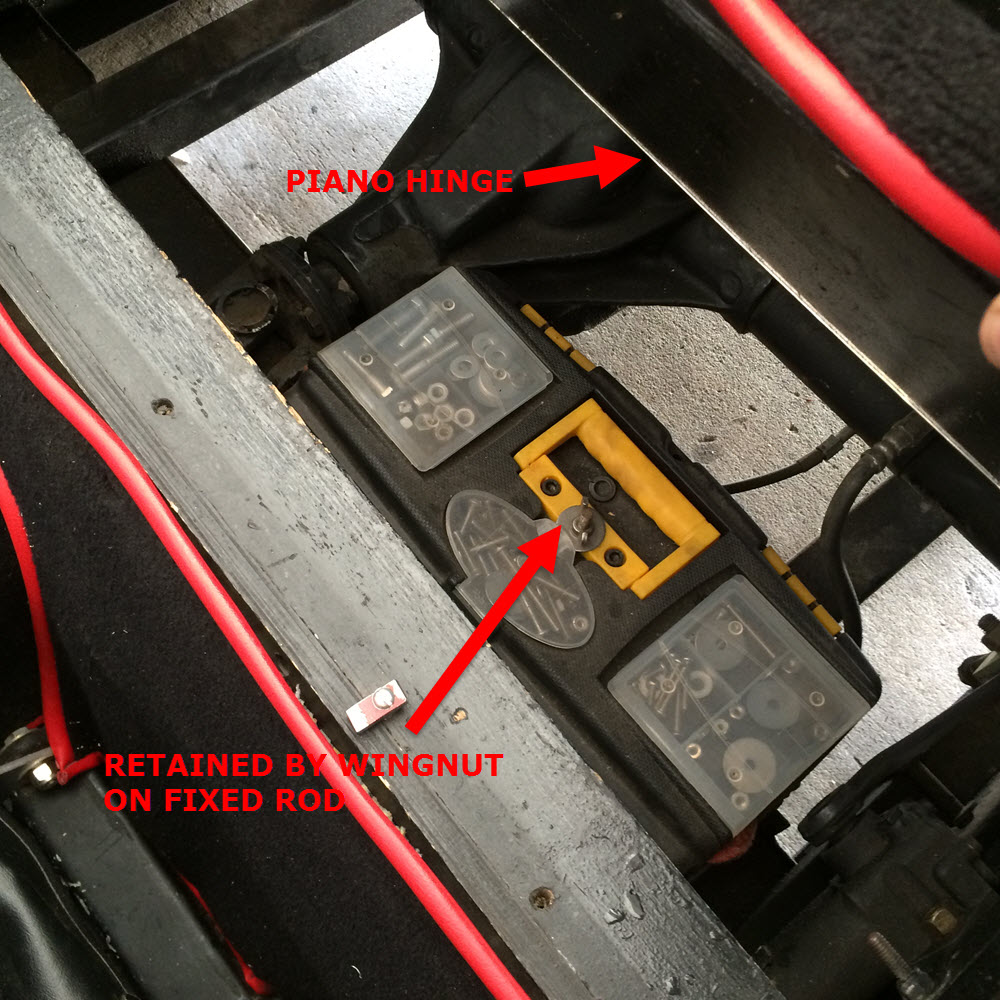
While not necessarily done for the upcoming European tour I did add a small toolbox from Harbor Freight under the package shelf, in front of the axel. I cut the package shelf in half across the car and hinged it to make it easier to lift the front half and access the toolbox that I hope to forget is even there. This space also stores my trailer tow-bar.
LUGGAGE:
On our last visit to Europe with a Morgan we did not have any problems with leaving the luggage strapped to the rack with bungee cords. That does seem like tempting fate though. I feel I have a minimum responsibility to make it somewhat difficult to steal my stuff. My luggage rack is a home-made prototype that I liked well enough not to bother making another version. I added an additional upright on the center bracket and a threaded nut for a long wing-screw similar to the one that holds the spare. The longer wing screw passes through a cross bar, through the handles of the carry-on bags and has a lock to keep it all in place against a less than well equipped thief. When the luggage is not on the car, like for shipping, a short screw locks the crossbar in place. Spiffy indeed!
PARCEL SHELF COVER
All modern hatchbacks come with a privacy cover over the boot area. I figured that the parcel shelf of the DHC will be filled with personal stuff that I would rather not have walk away. I made a cover of topping material and snapped it to an ash bar bridging the span between the wheel arches. There is a gap of several inches to allow the rear window to lie against the back wall of the parcel shelf. The canvas stretches over the standard ash bar behind the seats and clips to a hook on top of the drive shaft cover. the forward most edge of the cover is hemmed and hides a 1″ wide ash batten and the attachment to the hook is by bungee so it stays taut. I like it.
CENTER TAIL LIGHT
The need seems obvious doesn’t it.
Only problems were the gas filler neck and having luggage on the rack. A LED light from Moss and a home-made aluminum plinth solved both. Rather too soon the chrome started pitting. Experienced the same failure on several other cars I fitted these lights to. Wouldn’t use the Moss part again.
POWER OUTLETS
GPS and charge phone at the same time. Negative ground required.
COLUMN MOUNTED, SELF-CANCELLING DIRECTIONAL SWITCH
This has nothing to do with the trip to Europe but it is a most worthwhile modification. No more eternally flashing directional lights. The basic unit is adapted from a TR6. I tried several solutions for self-cancelling but all failed after brief use. I still use it since the stalk is still much more convenient than the center switch. The electric fan switch now fills the original hole in the dash panel.
UMBRELLA
Totally frivolous but fun. While in Europe we met some people from the Irish Morgan Club. They all had tubes with umbrellas attached to their luggage rack. Great idea. Mine is 3″ diameter aluminum tube from McMaster-Carr with end caps I turned from 1 1/2″ thick aluminum. We actually used it when caught in a downpour in Gettysburg at MOG 45. Parked, swooshed out the ‘brawlie and walked to the restaurant in style; almost dry.
center tail light